Minimize energy waste caused by unexpected heater burnout Monitoring of electric heaters degradation enhance energy efficiency and contribute to cost savings
- Heater failures lead to unexpected downtime. Stopping production, switching off the oven, and inefficiently reheating it consume additional energy.
- Replacing a failed heater and waiting for warm-up is time-consuming if not scheduled. Production halts during this period, affecting productivity.
- Current planned maintenance processes for heaters are labor-intensive.
Protect critical equipment from failures caused by DC loads malfunctions or power outages
A multitude of interconnected components, making it difficult to pinpoint specific issues when this is generated by a derating in the Power source.
- Concurrent activation of DC loads and unmanaged inrush currents or short circuits can lead to high current phenomenon affecting overall system stability.
- Unexpected power outages disrupt production processes, leading to lost time, scrapped products, and missed shipment dates.
Minimize the risk of electrical fires
Continuing to monitor the temperature panel remains a crucial step in fire prevention.
- Faulty electrical equipment or installations can lead to fires. Malfunctioning systems, short circuits, and electrical arcs are common causes.
- Loose electric connections can pose fire hazards, especially when equipment is subjected to vibrations during shipping and operation.
- Monitoring the temperature of critical components such as power distribution, transformers, or power supplies is not always practical.
Prevent unexpected breakdowns minimizing unplanned downtime
Multiple approaches to monitor different failures related to motor itself, the load and drive:
- abnormal load condition (foreign debris, pump cavitation);
- bearing wear malfunction (lack of lubrification);
- insulation degradation (dust intrusion, fluid leaking).
- Monitors strategic Drive components lifetime like fans, IGBTs, capacitors, etc…
Download our leaflets “Smart maintenance ideas and solutions’’ to learn more
-
Compact plug-in level controllers
-
Motor Condition Monitoring Device – current monitoring
-
Motor Condition Monitoring Device – vibration monitoring
-
Thermography-based Condition Monitoring
-
Condition Monitoring Device – insulation monitoring
-
Ultra-miniature liquid leakage sensor amplifier
-
Electric Heaters Condition Monitoring Device
-
Single-phase current relay
-
Single-phase current relay, window type
-
22.5 mm wide conductive level controller
-
3-phase asymmetry, phase-sequence, phase-loss relay
-
3-phase sequence, phase-loss relay
-
3-phase voltage, phase sequence, phase loss relay
-
3-phase voltage relay
-
Slim-line relays monitor three-phase motor temperature, phase sequence and phase loss.
-
Single-phase voltage relay
-
Single-phase voltage relay, window type
-
3-phase voltage asymmetry, phase sequence, phase loss
-
3-phase sequence, phase loss relay
-
3-phase undervoltage and phase-sequence phase-loss relay
-
Slim-line three-phase voltage, asymmetry and phase-sequence phase-loss protection
-
Single-phase current relay
-
Single-phase overcurrent/undercurrent relay
-
17.5 mm wide conductive level controller
-
Phase-sequence phase-loss relay
-
Three-phase voltage and phase-sequence phase-loss relay
-
Three-phase voltage, asymmetry, and phase-sequence phase-loss relay
-
Temperature monitoring relay
-
Single-phase voltage relay
-
Single-phase overvoltage/undervoltage relay
-
The Integrated AC Drivers Solution
-
Compact DC-DC UPS with DIN-rail prevents voltage drop and power failure in industrial PCs (IPC)/controllers
-
Switch Mode Power Supply S8VK-X
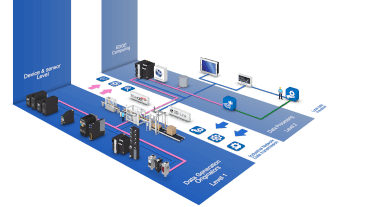
Back to Smart Maintenance
Maintenance is a vital to assuring 24/7 operations. Even the failure of a single component can have a massive impact on operations, while energy and maintenance expenses are a major part of the lifecycle costs of automatic machines
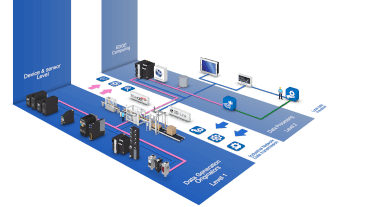
LEVEL 2: Elaborate Maintenance Data and information at the edge
Elaboration is done at machine level for quick reaction time and alerts.
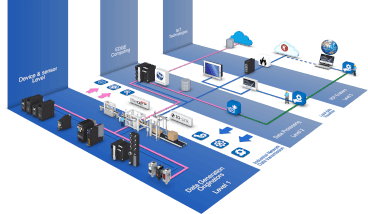
LEVEL 3: IoT enabler and Secure remote access
Reduced Spend on Site Maintenance Visits and cost optimisation.