Automation blog
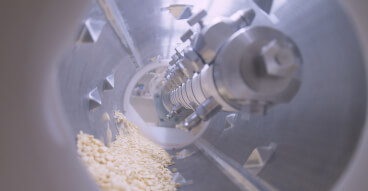
Unlock the Potential of UDI Compliance: Navigate the UDI Mandate with Confidence
08 January, 2024 Complying with the unique device identifier (UDI) system requirements is a critical milestone for medical device manufacturers, distributors, and end users. Ensuring compliance is not just about meeting a regulatory deadline; it's about safeguarding the integrity and safety of medical devices throughout their lifecycle in Europe and the United States.Our comprehensive whitepaper, "Ready for the UDI Mandate Deadline?" dives into the intricacies of UDI implementation, shedding light on the complexities beyond the surface. The ultimate goal is clear – to effectively identify and trace medical devices, from a simple bedpan to a lifesaving artificial heart, promoting safety across the healthcare landscape.However, the journey towards UDI compliance goes beyond merely affixing a printed barcode to a package. Establishing a robust system for verifying UDI markings, and ideally automating these processes, requires a thorough understanding of the means and methods involved. Inline verification during label generation and off-line validation in active service are pivotal components of a successful UDI system.In this whitepaper, we not only outline the UDI labeling requirements but also provide actionable insights into best practices. Discover how the medical device industry can ensure that marking methods are not only compliant but also meticulously verifiable. Elevate your understanding of UDI implementation and gain confidence in navigating the intricacies of the mandate.Don't miss out on this opportunity to empower your organisation with the knowledge needed to thrive in the era of UDI compliance. Download our whitepaper now to stay ahead in the evolving landscape of medical device regulations.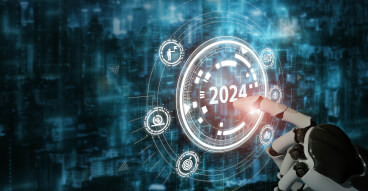
What’s in store for automation in 2024? Six predictions from OMRON Europe
13 December, 2023 The succession of shocks over the last few years has heralded a new era of heightened geopolitical and economic risk. This is prompting manufacturers to build resilience and flexibility into business models and rethink global supply chains and relationships. At the same time, pressure is mounting to incorporate ESG principles into operational decision making. AI, data science, digital twins and sensing, monitoring and vision technology will all be essential to developing automation and control solutions that can help the manufacturing industry adapt to this new reality. In this context, I would like to share the top six trends that will impact and shape industrial automation in 2024 and beyond.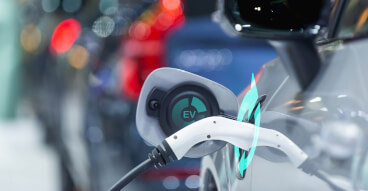
EV transition made easy: Top three challenges to overcome in automotive manufacturing
23 November, 2023 The transition to electric vehicles is a challenging path for automotive manufacturers. Long-established companies that have traditionally produced vehicles with combustion engines are now venturing into an entirely new realm of vehicle platforms. Let us investigate the top challenges facing the electric vehicle manufacturing industry and explore the latest innovative solutions on the horizon.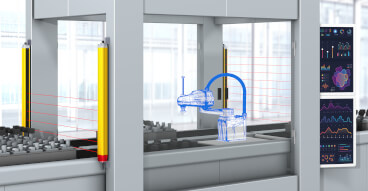
A meeting of minds: IT/OT convergence in industrial automation
22 September, 2023 Future-focused manufacturers are edging closer to their ideals of flexible, efficient and sustainable production by exploring digital transformation in earnest. However, as interest in digitalisation builds, it is becoming apparent that a huge gulf exists between the worlds of OT (Operational Technology) and IT (Information Technology). And this divide needs to be bridged if today’s visions for factories of the future are to become tomorrow’s reality.But before we look at why a convergence of IT and OT is necessary and how this can be achieved, let’s take a step back to basics and clear up some misunderstandings around the terminology.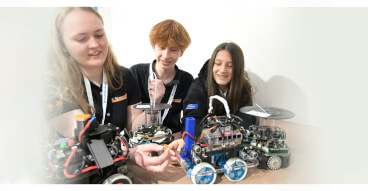
Empowering the workforce: OMRON's approach to skills development in European manufacturing
06 September, 2023 Delving into OMRON's unwavering commitment to nurturing skills that empower the next generation, while the industry embarks on a transformative journey – a journey that unlocks the full potential of the Fourth Industrial Revolution (4IR) while boldly moving towards the Fifth Industrial Revolution (5IR).In the halls of academia, the boardrooms of visionary business leaders, and the chambers of forward-thinking politicians, a fervent debate evokes. It revolves around the profound shift from the Fourth Industrial Revolution, 4IR, or Industry 4.0 as it is also known, to Industry 5.0 will change the world in which we live.Historically the Industrial Revolution was the First Machine Age, and electricity the Second, then electronics was the Third, and the internet as platform the Fourth Machine Age. We are now entering the Fifth Machine Age, which highlights harmonious human-machine collaboration and the contributions of the industry to society. This is the moment to not only adapt but to lead, to pioneer, and to create a future where innovation knows no bounds. Klaus Schwab, the founder and executive chairman of the World Economic Forum has observed that: “We stand on the brink of a technological revolution that will fundamentally alter the way we live, work, and relate to one another. In its scale, scope, and complexity, the transformation will be unlike anything humankind has experienced before. Our world is undergoing a transformative shift. Global production is evolving, driven by the automation of traditional industrial practices through smart technology, M2M communication, and IoT integration. This synergy fuels heightened automation, seamless communication, and intelligent machines that autonomously analyse and diagnose challenges.The rise of AI sparks debates, hinting at deeper transformations within our societal tapestry. As we navigate this dynamic landscape, we are poised to embrace innovation and reshape our future.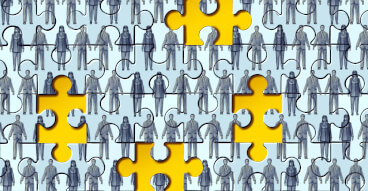
Top 4 Ways to Tackle Labour Shortage with Automation
06 September, 2023 Automation is a pathway to supporting manual workforce and not replacing them.Labour shortages in manufacturing are a growing cause of concern worldwide. While financial incentives and targeted workforce qualifications have been used as countermeasures, more innovative solutions are needed. Many manufacturers choose to automate repetitive activities but to what extent is it supporting the existing taskforce or is it taking away their jobs altogether?In 2023, Reuters disclosed an alarming trend: a record-high 53% of companies grapple with hiring difficulties. Staff shortages, soaring energy costs, combined with the pursuit of climate neutrality create new challenges. In the quest for sustainable manufacturing, innovative strategies to address labour gaps and enhance existing talent are the beacon of progress.Let us go over the top four ways to addressing the labour shortage and supporting the current workforce with automation: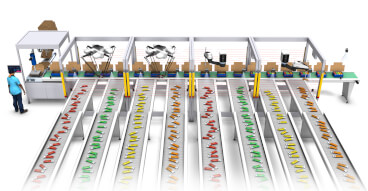
Easy programming
21 June, 2023 Omron Automation robotics are designed to be easy to program, even for users who have little or no experience with robotics. The robots can be programmed using intuitive software, and they can be taught new tasks through a simple "teach and playback" process. This makes it easy for manufacturers to integrate robotics into their production processes and improve their Pick & Place operations. With easy programming, manufacturers can reduce the learning curve and training time for operators, allowing them to get up and running quickly.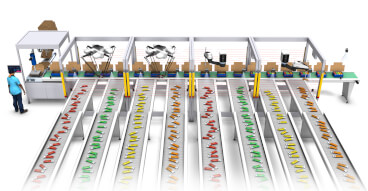
High-speed and precision movements
14 June, 2023 Omron Automation robotics are designed for high-speed and precision movements, which make them ideal for Pick & Place applications. The robots can pick up and place objects quickly and accurately, reducing cycle times and increasing productivity. Omron robots can move at high speeds without sacrificing precision, which is essential for Pick & Place applications where objects need to be placed in precise locations. With Omron Automation robotics, manufacturers can improve their production efficiency.Pick & Place applications are a common task in industrial settings, where objects need to be moved from one place to another quickly and accurately. This can be a repetitive and time-consuming task that can be automated using robotics solutions. In this blog post, we will explore how robotics can help with Pick & Place applications and improve productivity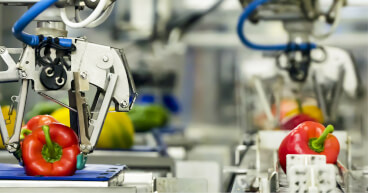
Flexible configurations
07 June, 2023 Omron Automation robotics can be configured in a variety of ways to suit different Pick & Place applications. The robots can be mounted on a fixed base or on a mobile platform, and they can be equipped with different end effectors to handle a wide range of objects. With Omron Automation robotics, manufacturers can customise the robots to meet their specific needs, allowing them to handle objects of different sizes, shapes, and weights.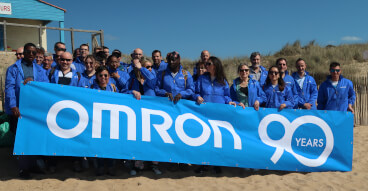
From red lights to robots: OMRON celebrates 90 years of innovation
06 June, 2023 This year on Founder’s Day, OMRON looked back on 90 years of pushing technological boundaries, and looks forward to a future of automation innovation framed by sustainability, digitalisation and human-machine collaboration.May the 10th be with you… Every year, 10th May is probably the most important day in OMRON’s calendar. On this day, 30,000 OMRON employees around the world celebrate the life and legacy of the company’s founder, Kazuma Tateishi. They do this by recommitting to Tateishi’s vision of using technology to create a better world and by giving back to society - often by participating in volunteer and charity projects in their communities. Innovation Milestones OMRON's journey of innovation began in 1933 with the development of a high-precision timer for X-ray photography. This marked the company's first contribution to addressing societal needs. In 1960, OMRON unveiled the world's first non-contact proximity switch, revolutionizing advanced mass production capabilities. Since then, OMRON has continued to introduce groundbreaking technologies, including the first automatic traffic signal, unmanned train station system, wearable blood pressure controller, ultra-high-speed fuzzy logical controller, and automatic cancer cell diagnostic equipment.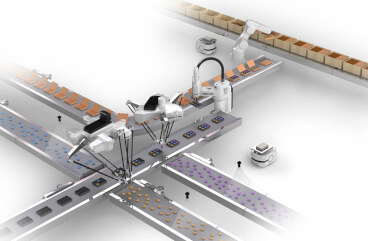
Collaborative capabilities
31 May, 2023 Omron Automation robotics can be used in collaborative applications, where they work alongside human operators to pick up and place objects. The robots are designed to be safe to work around, with sensors and other safety features that prevent collisions and other accidents. This allows manufacturers to use collaborative robotics in a wide range of applications, improving productivity and efficiency while maintaining a safe work environment. With collaborative capabilities, manufacturers can take advantage of the benefits of automation while still maintaining a human touch in their production processes.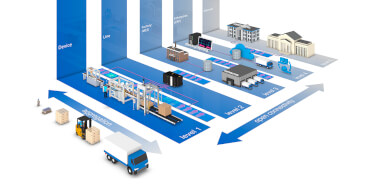
Transitioning from manual record keeping to fully automated traceability
11 May, 2023 In the fifth and final blog in this series on Traceability we will discover how machine vision technology has been taking on an increasingly important role in traceability because thanks to its effective way of maintaining complete product integrityVision inspection includes a wide variety of functionality such as detecting defective products in real time and performing both OCR and OCV to verify that the data on labels and packages adds up. By functioning as a complete solution for ensuring that non-conforming products don’t go out into the market, vision systems are vital for brand protection.The hurdle that manufacturers face in implementing a machine vision system is twofold. Such systems are often expensive to implement, and the complexity of the technology can overwhelm operators. Many applications require special programming. However, these challenges are offset by the fact that a single product recall or fine for tainted product – preventable by a vision system – could cost more than the vision system itself.The avoidance of unwanted complexity isn’t just a deterrent to using machine vision – it’s often a reason why manufacturers forego upgrading their traceability systems in any way. Because implementing a new system seems inordinately complex, many manufacturers prefer to stick with cumbersome and error-prone record keeping methods that rely on manual processes. It’s understandable that companies want traceability to be easy. However, failing to upgrade the system with automation actually leads to more work in the long run.Manual record keeping is far more widespread in the food and beverage packaging industry than it should be, especially when one considers the huge costs associated with certain types of mistakes. Unfortunately, not all companies have the budget to invest in good traceability software. Budgetary constraints and the fact that traceability solutions need to be scalable are major barriers to automating the system.OMRON strives to make traceability as easy as possible, just as it strives to make its machine vision technology intuitive enough for the average operator to use. Its MicroHAWK barcode readers keep things simple by working right out of the box – in fact, the browserbased WebLink interface allows manufacturers to start using the readers without needing to install any software whatsoever. OMRON also has extensive knowledge of how traceability works in a variety of industries, and its focus on providing comprehensive solutions with complete line integration lets companies rest assured that the upgraded system will “just work.”Although often perceived to be challenging and somewhat expensive at the outset, a robust traceability system is the single most important means of complying with industry regulations and reducing the incidence and cost of recalls. OMRON’s traceability solutions address various pain points that manufacturers face in the food and beverage packaging industry so that real-time, automated traceability is within the reach of any company that needs to comply.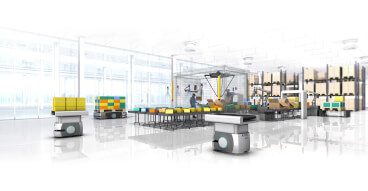
Mastering packaging and intralogistics challenges in eCommerce
24 February, 2022 Robot-assisted packaging enables fast and cost-efficient scalability upward and downward to handle swings in demands from the supply chain.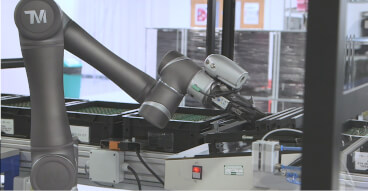
Hanover Displays automates PCBA testing with cobots
31 January, 2022 UK-based Hanover Displays Limited needed a new system for testing printed circuit board assemblies (PCBAs) and selected OMRON TM cobots for the job, supplied and installed by Absolute Robotics, part of the Absolute Automation Group.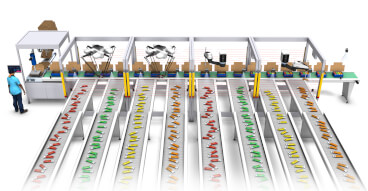
Five challenges in High-Mix, Low-Volume (HMLV) packaging and palletizing processes
21 December, 2021 The new product has just left the factory, in a shelf-ready package in the specified mixed ratio to meet customer needs. The packaging has actually been handled by another company: a co-packer. Co-packing can be found in all Fast-Moving Consumer Goods (FMCG) markets, but especially in the higher-priced product segments such as personal care or confectionery, to name a few examples. It is a fast-growing activity to satisfy the consumer demand for more variety.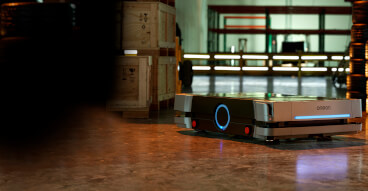
Rethink your Company’s Intralogistics Approach with Autonomous Mobile Robots (AMRs)
09 December, 2021 Intralogistics refers to the management and movement of materials and goods within a facility, and whether it is a warehouse, distribution centre, factory, or another production facility, it can be a significant hurdle to overcome. But by investing significant time and effort into your facility’s intralogistics, you can: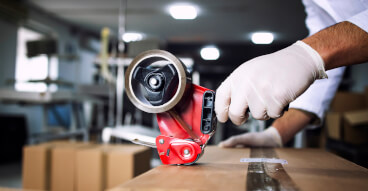
How Automating Tasks like Case Packing is the Logical Response to Record Vacancies
02 December, 2021 The UK is experiencing significant labour shortages across multiple industries. Brexit combined with the pandemic led to total UK job vacancies passing 1 million for the first time on record, and the food industry is one of the hardest-hit sectors. A lack of staff to call upon puts considerable strain on our food supply and creates headaches for employers around the country.Within the food industry, much of the focus has been on the shortage of lorry drivers and how this is causing higher food prices. However, a lack of staff is being felt across the industry in production, fruit/veg picking, packaging, and more.Strict travel restrictions due to Covid combined with Brexit means jobs previously performed by overseas workers remain unfilled. Plus, the pandemic and a break from the usual work cycle lead many people to re-evaluate their profession and look for careers that offer them increased flexibility and autonomy over when and where they work.A significant portion of the food industry vacancy problems is in less desirable positions that are low wage and physically demanding. Fortunately for employers, many of these jobs are ideal candidates for automation. Case packing is a great example of this.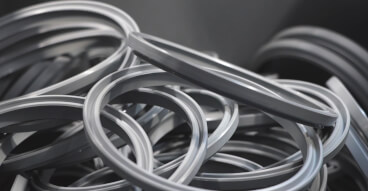
Finished seals in less than 10 seconds: Robotics Integrated Controller ensures harmonious control
24 November, 2021 Trelleborg Livorno has updated a robotic cell for the finishing of polyurethane gaskets for the sustainable wind energy market. The cornerstone of the solution is OMRON's Robotics Integrated Controller that ensures integration and synchronization of all automation components, including robots, logic, motion, safety and user interface.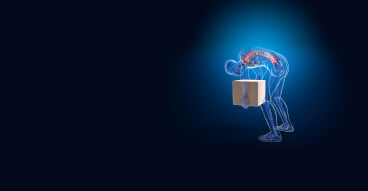
The Pitfalls of Manual Handling in End of Line Applications and Why Automation Is The Solution
18 November, 2021 No matter the industry you operate in, packaging, managing, and getting your inventory to where it needs to be is a significant headache. Businesses require robust and agile palletising processes that maximise efficiency, eliminate costly errors, and integrate seamlessly within wider workflows.Automating your end of line applications offers a range of tangible business benefits to increase output, reduce costs, and give your company a real competitive advantage.In the past, implementing new automated systems has been seen as too complex a process. The learning curve of integrating an entirely new system has appeared too steep to reach the benefits on the other end.But with new collaborative robotic systems, like the RB1200 Cobot Palletiser from Omron, automating your end of line processes has never been simpler. The RB1200 provides versatile and straightforward solutions for your palletising needs. The plug and play system with intuitive visual software can be configured in minutes to match the product and configuration you require.With advanced automation solutions for end of line applications, your business can simplify stock management and avoid the pitfalls associated with manual handling.Companies that rely on manual handling to stack and transport their goods are doing business on hard mode, making a complex task more difficult. The downsides of utilising manual handling in your end of line processes include: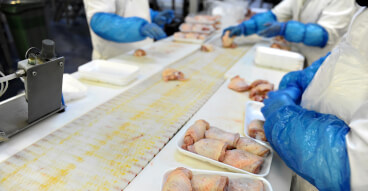
Digitally Transform your Food Production Line using Smart Pick and Place Robot
17 November, 2021 A once in a generation labour shortage has put the UK food industry in a precarious position. Through a combination of Covid and Brexit, fewer workers being available is placing significant strains on food production and supply chains. A lack of:Delivery driversProduction line workersFruit pickersAbattoir staffAnd other workersHas led to instances of empty supermarket shelves with a growing number of missed food deliveries. Our food supply chains are beginning to feel the bite.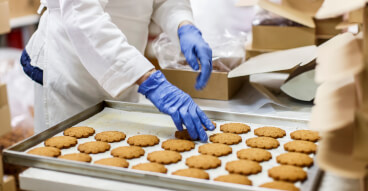
Manual Tasks in Manufacturing: Risky? Expensive? Both!
04 November, 2021 There are fewer people employed in the manufacturing sector now than at any other point in the last 25 years!! According to the Office for National Statistics, the 6- month period between October 2020 and April 2021 saw the lowest level of employment in the manufacturing sector since 1996. Conversely, consumer demand is at an all-time high. The impact of this is acutely felt in the food industry where a severe shortage of workers has led to unprecedented levels of job vacancies..
FasThink optimizes Garnet's intralogistics with mobile robots
02 November, 2021 Garnet relies on FasThink to innovate its logistics and production processes.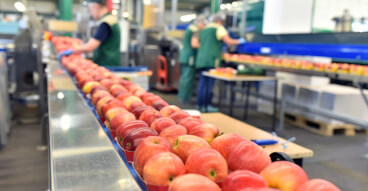
Automation and the human touch
27 October, 2021 Ensuring products are sorted correctly and placed in the correct orientations are critical functions when preparing food and other consumer goods to be packaged and ready for consumption. Imagine if a multipack of peppers had 3 green ones; or if a pack of pancakes had 2 missing because they were outside of the range of the flow-wrapper. Doubtless, we wouldn’t be too happy. Even worse, we can’t get hold of the products we want because there is a large scale shortage…
Intelligent System Solutions with Autonomous Mobile Robot: AM-Flow and OMRON
27 October, 2021 Industry 4.0 brings the promise of streamlined processes, big data insights and production lines running 24/7 with zero downtime. Unlike historical ‘industrial revolutions,’ this one offers the luxury of time and choice for manufacturers. That’s because the benefits of automation can be embraced incrementally or fully, whether it’s a new state-of-the-art facility or something retrofit-installed into a more traditional production setup. Making it easier to make the move is AM-Flow, an entrepreneurial start-up currently making waves in providing its solutions to the new tide of producers coming ashore in the world of additive manufacturing.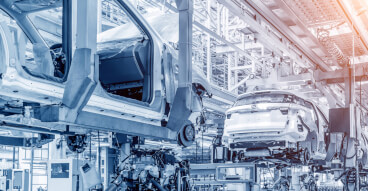
Where is the future heading, intralogistics? Tips for more efficiency
15 November, 2022 Sometimes we focus so much on the big picture that we forget the smaller and yet so important processes that characterize smart production. One example is intralogistics, i.e. the flows of materials and goods that take place on a company's premises or in a production hall. A recent study found that more than 80 percent of the companies surveyed consider the increased use of AI and automation in intralogistics to be necessary to meet challenges such as the shortage of skilled workers or growth plans.Automotive companies that want to meet market and customer requirements, increase efficiency and become more sustainable must come up with new ideas. Energy costs, the gas crisis, and rising inflation make this task even more difficult. Smart factory concepts that combine innovative automation, digitalization, and smart intralogistics approaches can provide valuable support. Some speak of Industry 4.0 in this context, others of the “factory of the future”, still others prefer Industrial Internet of Things (IIoT). But no matter which term you favor: The most important thing is to become active now and to rely on reliable partners. Intralogistics is a good starting point for quickly initiating change. Because action is urgently needed: many companies are currently severely limited due to the shortage of skilled workers. Modern technologies such as mobile robots can provide a remedy.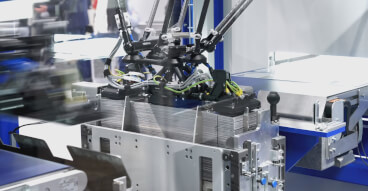
Digitalization in the automotive industry: Seven tips for smart production
02 November, 2022 If you want to grow and master crises, you have to be digitally fit – this also applies to the important automotive sector. There is no way around digital tools for addressing customers or productivity. Artificial intelligence (AI) and sustainability are key drivers and focus topics, as a study by Capgemini shows. Experts from Gartner point out the importance of open-source collaboration approaches, holistic ecosystems, and technology partnerships. But what should we look out for in digitalization and intralogistics in the production of the future? We want to answer this question in two parts. We start with tips on digitization in the smart factory. As an automation expert, OMRON has been accompanying manufacturers and suppliers on their way to more digitalization sophistication for many years.
Artificial Intelligence: hope, hype and FOMO
22 September, 2022 Ten years ago when we received enquiries about AI-based projects, they were mainly driven by hype or FOMO. When I asked why they wanted to get into AI, the answer, more often than not, was either ‘because my boss asked me to’, ‘because we have a lot of data’ or ‘because it seems like an interesting area’. None of these were particularly solid reasons and certainly didn’t justify the hefty investment that AI applications would have required at that time.That is changing, and hope, rather than hype or ‘FOMO’, is the driver. Customers don’t ask whether we can help them with AI anymore. They ask us whether we can help with predictive maintenance, quality control or process optimisation. They come to us with a problem that they want us to help solve. The adoption of AI is no longer a motive or an aim in itself. Instead, AI has become an ‘enabler’.Whatever the industry - whether food & drink, pharmaceutical, electronics or automotive - the end goal is the same: producing high quality, defect-free products at a lower cost, using less energy and less labour. And AI can be one of a suite of solutions for achieving those objectives.
Automation adapts to sustainable packaging
16 August, 2022 Have you ever ordered a small item online, and then felt incensed when it arrived in an oversized box packed out with bubble wrap, air-filled cushions or paper inserts?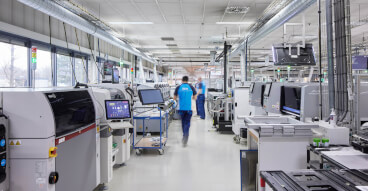
Building the Factory of the Future together
16 June, 2022 As one of the largest business units at OMRON, we aim to further develop the Den Bosch plant to serve the needs in the EMEA region.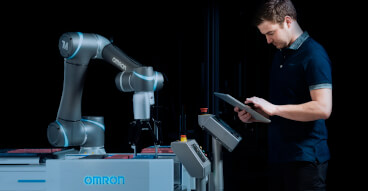
Lights out? Still unlikely with Industry 4.0
21 April, 2022 For many manufacturers, the prospect of a fully automated, human-free factory feels light years away. When, they ask, is the 4th Industrial revolution coming to us and what can we expect? In this blog, we look at the realities of (fully-/semi-)automated manufacturing, what robots can and can’t do, and why the human touch is still (mostly) irreplaceable.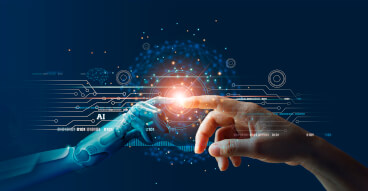
Traditional factories have data needs too
18 March, 2022 The right tools and tech can enable advanced predictive maintenance, bottleneck prevention and optimization. Find out how digitalization is bridging the gap between legacy systems and Industry 4.0.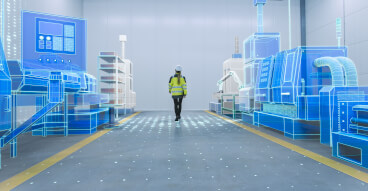
Productivity Peaks: Moving Maintenance From Preventive to Predictive
17 December, 2021 Maintenance is a vital key to a thriving business, especially in manufacturing where 24/7 plant equipment uptime is often expected as standard. As any established enterprise knows, keeping production lines and systems running optimally requires more than a skilled maintenance team. It also involves careful planning, tight scheduling, constant vigilance, a willingness to change out unworn parts, and a readiness to respond to unplanned events. At least, it used to.
Developing digital capability: how any factory can be smart
16 September, 2021 Thankfully, the headline-grabbing ‘Industry 4.0’ isn’t reserved exclusively for the high-tech giants that span the globe, nor is the term ‘smart factory’ applied only to brand-new installations. In truth, any traditional factory can in principle take steps on the smart factory journey, by applying modularity to the existing installation.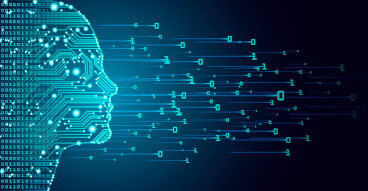
Monitor machine stability with data science
16 July, 2021 Do you have a machine with no problems? You’re probably already collecting production and machine data, but not using it. With a quick scan of your data, it is possible to judge the usability and quality of the data and start using the value inside the data. This will help you define the first or next step towards a data enabled organization.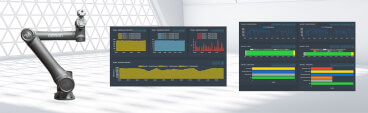
Cobot Dashboard: How to visualize data for OEE improvement the smart way
16 March, 2021 The factory of the future is not only based on a well-orchestrated interaction of the most diverse machines, robots, sensors, and AI technologies. Entrepreneurs and decision-makers are also increasingly faced with the challenge of reconciling the vast amounts of data collected by the various production lines and making the best possible use of it to support their decisions. Not only does a comprehensive data strategy need to be developed. There are also technologies required that process and present the data in such a way that issues are immediately identified before major problems occur.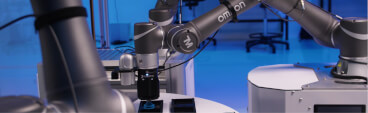
Developing smart and flexible production: Norwegian university sets up new manufacturing lab packed with robots
10 February, 2021 The Norwegian University of Science and Technology (NTNU) has developed a new educational laboratory in Ålesund to facilitate learning and extend the implementation of automation and robotics amongst manufacturers in the region. The lab is packed with a wide range of OMRON solutions – both hardware and software.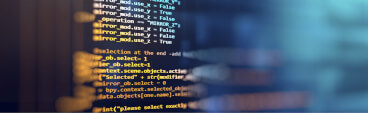
Solving machinery downtime challenges with remote connectivity
07 February, 2023 Manufacturing machinery is a significant investment and every minute it isn’t running is a lost opportunity for your business. Studies show that unexpected machinery downtime costs industrial manufacturers an estimated $50 billion (USD) each year, and poor maintenance strategies can reduce capacity by 5 to 20%.With money on the line, organisations require production schedules that minimise downtime while still allowing for critical maintenance to ensure safety.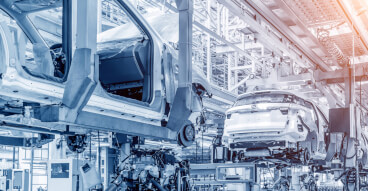
Where is the future heading, intralogistics? Tips for more efficiency
15 November, 2022 Sometimes we focus so much on the big picture that we forget the smaller and yet so important processes that characterize smart production. One example is intralogistics, i.e. the flows of materials and goods that take place on a company's premises or in a production hall. A recent study found that more than 80 percent of the companies surveyed consider the increased use of AI and automation in intralogistics to be necessary to meet challenges such as the shortage of skilled workers or growth plans.Automotive companies that want to meet market and customer requirements, increase efficiency and become more sustainable must come up with new ideas. Energy costs, the gas crisis, and rising inflation make this task even more difficult. Smart factory concepts that combine innovative automation, digitalization, and smart intralogistics approaches can provide valuable support. Some speak of Industry 4.0 in this context, others of the “factory of the future”, still others prefer Industrial Internet of Things (IIoT). But no matter which term you favor: The most important thing is to become active now and to rely on reliable partners. Intralogistics is a good starting point for quickly initiating change. Because action is urgently needed: many companies are currently severely limited due to the shortage of skilled workers. Modern technologies such as mobile robots can provide a remedy.
Artificial Intelligence: hope, hype and FOMO
22 September, 2022 Ten years ago when we received enquiries about AI-based projects, they were mainly driven by hype or FOMO. When I asked why they wanted to get into AI, the answer, more often than not, was either ‘because my boss asked me to’, ‘because we have a lot of data’ or ‘because it seems like an interesting area’. None of these were particularly solid reasons and certainly didn’t justify the hefty investment that AI applications would have required at that time.That is changing, and hope, rather than hype or ‘FOMO’, is the driver. Customers don’t ask whether we can help them with AI anymore. They ask us whether we can help with predictive maintenance, quality control or process optimisation. They come to us with a problem that they want us to help solve. The adoption of AI is no longer a motive or an aim in itself. Instead, AI has become an ‘enabler’.Whatever the industry - whether food & drink, pharmaceutical, electronics or automotive - the end goal is the same: producing high quality, defect-free products at a lower cost, using less energy and less labour. And AI can be one of a suite of solutions for achieving those objectives.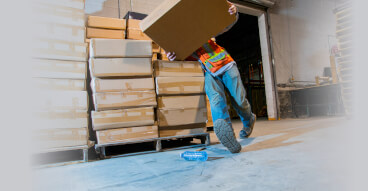
How the RB1200 Cobot Palletiser Can Simplify Your Automation Deployment
13 April, 2022 Greater automation and collaborative robotics (cobots) are the future for many industries, including logistics. Research by BMW found humans and robots work more than well together. In fact, human-robot teams were 85% more productive than working alone.It makes sense. Combining the speed and accuracy of robotics with the flexibility and intuition of humans compounds the benefits from each to build an unbeatable team.With the RB1200 Cobot Palletiser, OMRON, in collaboration with Reeco, is bringing a revolutionary new approach to end of line palletising. Creating an easy, flexible, safe, and compact solution to getting stock palletised and ready for transport.Palletising is a task perfectly suited to automation. The simple yet repetitive and physically demanding process of getting goods stacked leads to complications when performed manually. In 2019/2020, the Health and Safety Executive (HSE) estimated 19% of non-fatal workplace injuries were caused by handling, lifting, and carrying.Plus, given the labour shortages facing the UK and the wider world and the potential for spiralling staff costs, now is the ideal time to get your company less reliant on manual labour.While there are plenty of benefits to automating your palletising processes (greater output and accuracy, reduced labour and operational costs, etc.), its implementation also has challenges.However, with the RB1200 Cobot Palletiser, humans can collaborate with robotics on their terms, implementing a solution that fits their specific needs.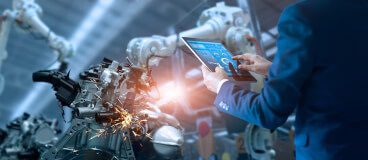
Discover How The CP1200 Case Packer Can Transform Your End-of-Line Manufacturing Processes
29 March, 2022 By Stuart Coulton, Market Development Manager, OMRON UK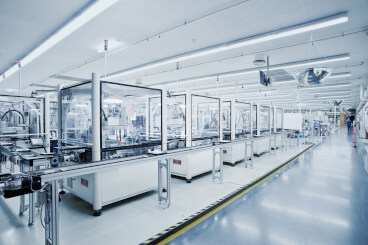
End of Line Automation: Now is the Time!!
29 March, 2022 By Stuart Coulton, Market Development Manager, OMRON UK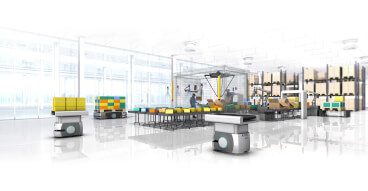
Mastering packaging and intralogistics challenges in eCommerce
24 February, 2022 Robot-assisted packaging enables fast and cost-efficient scalability upward and downward to handle swings in demands from the supply chain.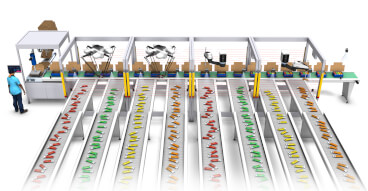
Five challenges in High-Mix, Low-Volume (HMLV) packaging and palletizing processes
21 December, 2021 The new product has just left the factory, in a shelf-ready package in the specified mixed ratio to meet customer needs. The packaging has actually been handled by another company: a co-packer. Co-packing can be found in all Fast-Moving Consumer Goods (FMCG) markets, but especially in the higher-priced product segments such as personal care or confectionery, to name a few examples. It is a fast-growing activity to satisfy the consumer demand for more variety.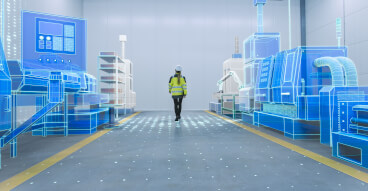
Productivity Peaks: Moving Maintenance From Preventive to Predictive
17 December, 2021 Maintenance is a vital key to a thriving business, especially in manufacturing where 24/7 plant equipment uptime is often expected as standard. As any established enterprise knows, keeping production lines and systems running optimally requires more than a skilled maintenance team. It also involves careful planning, tight scheduling, constant vigilance, a willingness to change out unworn parts, and a readiness to respond to unplanned events. At least, it used to.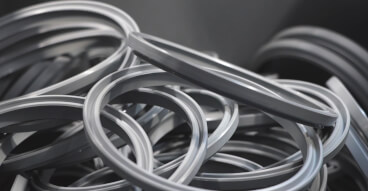
Finished seals in less than 10 seconds: Robotics Integrated Controller ensures harmonious control
24 November, 2021 Trelleborg Livorno has updated a robotic cell for the finishing of polyurethane gaskets for the sustainable wind energy market. The cornerstone of the solution is OMRON's Robotics Integrated Controller that ensures integration and synchronization of all automation components, including robots, logic, motion, safety and user interface.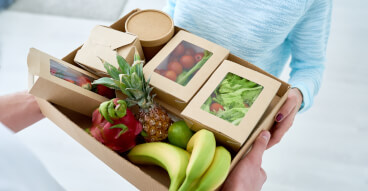
Plastics in consumer goods manufacturing: Seven automation tips for greener packaging
29 April, 2021 Hygiene or environmental protection? Preferably both! Companies in the consumer goods industry are increasingly asking themselves what alternatives they have to plastic packaging and how they can act greener, more efficiently, and yet still safely. Innovative packaging lines, robotics and artificial intelligence offer support.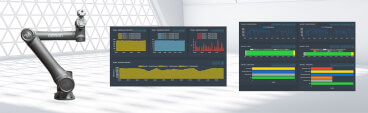
Cobot Dashboard: How to visualize data for OEE improvement the smart way
16 March, 2021 The factory of the future is not only based on a well-orchestrated interaction of the most diverse machines, robots, sensors, and AI technologies. Entrepreneurs and decision-makers are also increasingly faced with the challenge of reconciling the vast amounts of data collected by the various production lines and making the best possible use of it to support their decisions. Not only does a comprehensive data strategy need to be developed. There are also technologies required that process and present the data in such a way that issues are immediately identified before major problems occur.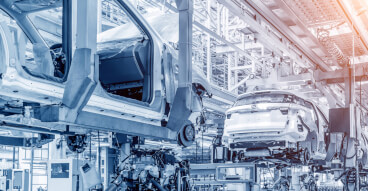
Integrated data control, motion control and machine vision for next-generation automotive production line
24 April, 2020 The Mexican regional headquarters of a leading manufacturer of premium air brake actuators for global on-highway and specialty markets required a new automated production assembly line. One of the company’s key performance indicators is to deliver a fully assembled product every 30 seconds, and it is with this end goal at the forefront that the team started the process of automating the production line.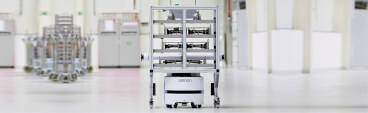
ŠKODA AUTO uses LD mobile robot at Vrchlabí plant
17 March, 2020 The autonomous robot contributes to the continuous improvement of work safety in Vrchlabí and helps to minimise work risks. It recognises people crossing its path as well as other vehicles and stationary obstacles.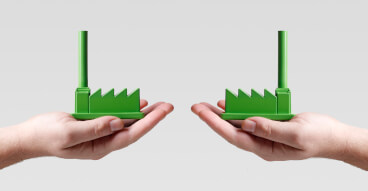
Green is key: sustainability in battery manufacturing for E-mobility
05 February, 2020 Today, sustainability is no longer a niche topic, but something that companies are integrating into their business strategies. Not only are sustainability practices necessary to answer the changing demands of consumers, the marketplace and governments, they are also increasingly being seen as a competitive strength. That’s because sustainability practices reduce energy consumption and waste, and also help companies use their resources more efficiently. They even help companies optimize their manufacturing agility and enable them to respond to fluctuating demand and the growing need for personalization. And finally, sustainability can play an important role in acquiring and retaining customers, as well in developing new market opportunities.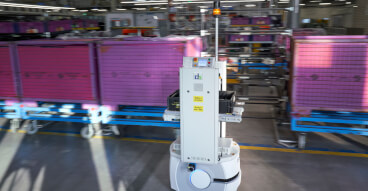
Agile and clever tailor-made mobile robotics
04 November, 2019 Major German automotive group optimizes efficiency and innovation leadership in material handling with Omron LD mobile robots and a conveyor attachment from cts GmbH.Automobile production and assembly line production have always been closely linked. It was not until Henry Ford began using conveyor belts in his factories in 1913 that the car was able to conquer the world as a mass-produced product. Today, a working day without assembly lines is inconceivable at the BMW factories. The group relies on innovative transport and logistics to increase efficiency and flexibility, to better link work processes, as well as to relieve employees from repetitive and time-consuming tasks. These concepts include Omron LD mobile robots for material transport that deliver a particularly high return on investment (ROI). These autonomous mobile robots are equipped with a conveyor tower - a height-adjustable load handling device, developed by system integrator cts GmbH. The interaction between employees and transport robots at BMW impressively demonstrates how factory harmony can be implemented in the factory of the future.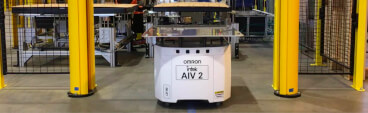
Mobile robots speed production at new ‘smart factory’
26 September, 2019 Showcasing flexible production in real life, a new ‘Smart Factory’ in Norway uses a variety of robots in a system developed and implemented by system integrator Intek Engineering.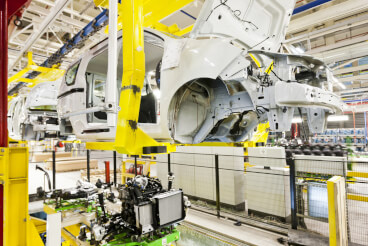