Solving machinery downtime challenges with remote connectivity
Published on 07 February, 2023 in Industry 4.0
How remote connectivity can reduce machine downtime
Manufacturing machinery is a significant investment and every minute it isn’t running is a lost opportunity for your business. Studies show that unexpected machinery downtime costs industrial manufacturers an estimated $50 billion (USD) each year, and poor maintenance strategies can reduce capacity by 5 to 20%.
With money on the line, organisations require production schedules that minimise downtime while still allowing for critical maintenance to ensure safety.
Common causes of machine downtime
There are many reasons why operations may grind to a halt. These include:
Malfunctioning equipment
Manufacturing places significant stresses on machinery, making it susceptible to wear and tear, overheating and general failures. Malfunctions are a part of operations, and manufacturers need a staff of experienced individuals capable of maintaining equipment, diagnosing problems, solving minor issues, and calling in more experienced engineers when required.
Labour shortages
Sometimes, the machinery is working fine; there just aren’t enough people to run production safely. UK labour shortages have been at record levels since the pandemic, with data from the summer of 2022 estimating the UK manufacturing industry has 95,000 vacancies, equating to roughly £7 billion in lost output.
Human error
Not everything goes according to plan, and mistakes occur on the manufacturing floor, especially when employees work long shifts doing monotonous tasks. Human errors can lead to minor malfunctions that only require quick fixes to get back up and running or, in exceptional circumstances, significant breakdowns that lead to lengthy and expensive repairs
Resources/inventory being unavailable
Running machinery is redundant without the resources and inventory to produce what is necessary. With growing supply chain issues over recent years, it is becoming harder to maintain an inventory capable of improving output and meeting demands.
Poor maintenance planning
All machinery needs regular maintenance and servicing. When performed properly, planned maintenance can minimise machine downtime and prevent significant ripple effects that reduce output. With a poor strategy for maintenance and repairs, machinery can become unavailable at critical times, such as when a full shift of employees is ready to go, or the facility is pushing to meet an important deadline.
Regardless of the reason, manufacturers need plans in place to reduce the likelihood of machines going down. Thankfully, businesses can take a more sophisticated approach to managing their equipment.
What is remote connectivity?
Remote connectivity offers the ability to dial into automated systems and access machinery data. Modern manufacturing equipment generates a significant amount of critical data that businesses can tap into to improve operations. With remote connectivity, this data is accessible regardless of location, so:
- Management can receive production data and tweak schedules while being away from the facility
- Engineers can check machinery performance and adapt maintenance plans remotely, minimising expenses and reducing the need for costly service engineer trips
- Businesses can even set triggers based on specific data, i.e., machinery is overheating, the output is dropping and requires investigation, etc.
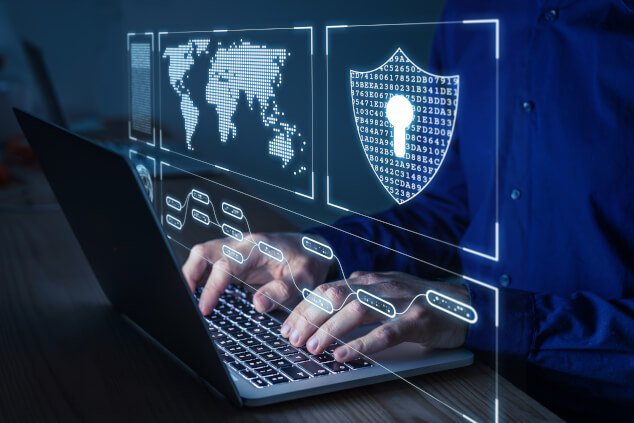
Five challenges to solve when using remote connectivity
- Preventing hacking and malware
Greater connectivity helps get data to the people and systems who can make a difference and positively impact operations. Unfortunately, it also has the potential to let bad actors into your network, causing havoc through a range of potential cyber attacks such as malware and ransomware. To protect your machinery, you should utilise a remote connectivity solution with stringent encryption protocols such as AES 256. This level of encryption ensures you get the best of both worlds. Remote access to all the devices (e.g., manufacturing machinery) on your network while keeping it protected from hacking or malware. - Service level agreements (SLAs) that don't limit service
With a remote access gateway utilising secure VPN-like access, it is possible to manage SLAs without restricting service. You no longer need to be present on a local machine, track your machinery data wherever you are safe in the knowledge that only trusted individuals have access. - Data ownership and control
Remote access can introduce data ownership and control concerns. An easy way to overcome these is to utilise a data management server operated by a secure third party. Consider remote connectivity solutions that provide LDAP (Lightweight Directory Access Protocol) and AD (Active Directory) integration and a custom DNS (Domain Name System). - Installing software onto machines
While remote connectivity can reduce machine downtime, implementing the technology requires installation and configuration. To minimise the impact, look for solutions that allow you to install remote connectivity tools on remote terminals, minimising the need for local access. This also enables support engineers to deploy tools remotely. - LAN and wireless connectivity
Modern remote access solutions offer flexibility when it comes to connectivity, with LAN or wireless options such as 4G and WiFi. Regardless of your setup, you can find a way to remotely access your machinery in a manner that is convenient for you.
Conclusion
Machine downtime is a major problem the manufacturing industry needs to overcome. With fewer employees and certainly fewer employees with the requisite skills, organisations must consider new approaches to maintaining and operating their machinery to maximise output.
Given the bleak economic output, UK manufacturers need to find new ways to minimise machinery downtime and the costs associated with it. While remote connectivity is not a new tool, it is increasingly important, offering efficient and seamless operations for businesses looking for more innovative ways to work.
Discover more with our new Remote Connectivity White Paper