Automation blog
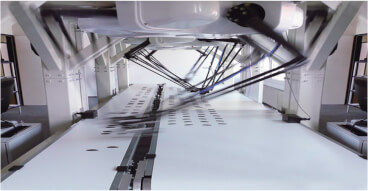
Introduction to Pick & Place applications and Omron Automation Robotics
08 May, 2023 Pick & Place applications are a common task in industrial settings, where objects need to be moved from one place to another quickly and accurately. This can be a repetitive and time-consuming task that can be automated using robotics solutions. In this blog post, we will explore how robotics can help with Pick & Place applications and improve productivity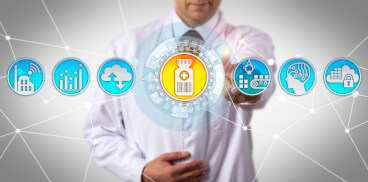
Using traceability to analyse and optimise productivity
04 May, 2023 In the fourth blog in this series on Traceability we will discover how the use of traceability can add value to the production process by optimising productivity.In addition to helping companies avoid recalls and other disruptions to their profitability, traceability systems are also a great way to optimise processes and evaluate overall equipment effectiveness (OEE). By collecting and analysing operational data, manufacturers can figure out which machines are under-performing and pinpoint precisely where bottlenecks are occurring in production.In order to gather this data, manufacturers need to set up numerous code reading stations at various points across the production line. Barcoding helps track vital productivity information such as throughput and quality based on package type, machine, shift and product. In many cases, this means that barcode readers need to be embedded within machinery. This poses a challenge, since most manufacturing equipment is designed to take up as little space as possible and therefore doesn’t have much extra room for barcode readers. This creates the need for ultracompact readers.These ultra-compact industrial barcode readers and smart cameras are designed to be highly flexible and configurable within an exceptionally compact casing. This means that they can be easily embedded within machinery while still providing fast and accurate reading. Thanks to their liquid lens autofocus technology, the readers eliminate constraints on camera positioning. The same camera can be used for machine vision inspection, enabling the expansion of automation as a facility’s needs evolve without investment in new hardware.Once traceability data is gathered via the barcode readers, it needs to be communicated to the rest of the system. This poses a new challenge – that of using this data without hampering control performance. When traditional controllers are tasked with processing large amounts of traceability data, they are liable to slow down the production cycle time.Automation manufacturers have addressed this issue by developing controllers that can maintain high-speed control while handling all the information a traceability system provides. For example, controllers can be used for a packaging machine with the capability of handling 1,000 products per minute and can collect all traceability data in synchronisation with the production cycle while performing motion control. This means that traceability doesn’t need to slow down other aspects of production while fulfilling the purpose of collecting important data. Barcode readers provide direct connectivity via Ethernet/IP to the controllers, making it simple to integrate traceability data into the automated system. When it comes to utilizing traceability information, the data collection is one challenge. It’s another matter altogether to transfer that data to the business and enterprise systems that store and use the data. Controllers can make this easy thanks to the seamless incorporation of SQL and OPC-UA.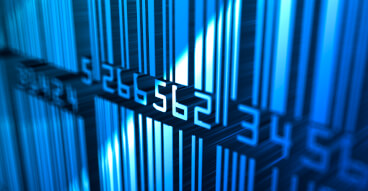
Combatting counterfeiting, promoting ethical sourcing and minimising recalls
26 April, 2023 In the third blog in this series on Traceability we will discover how counterfeiting has become a major issue in the food and beverage sector and how effective labelling can aid in a host of verification related tasks.Counterfeiting has become a major problem in the food and beverage industry as the market becomes more globalised. Several types of fraud exist, they can appear alone or in a combination in food fraud.Dilution - mixing a liquid ingredient of high value with a liquid of lower value.Substitution - replacing an ingredient, or part of the product, of high value with another ingredient, or part of the product of lower value.Concealment - hiding the low quality of food ingredients or product.Mislabelling - placing false claim on packaging for economic gain.Unapproved enhancement - adding unknown and undeclared materials to food products to enhance the quality attributes.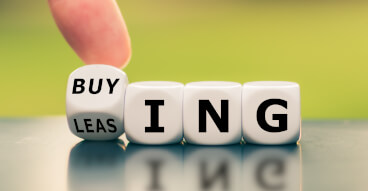
Buying or Leasing? How to finance your new cobot
26 April, 2023 Food for thought for SMEs when funding automation projectsSkills shortages, digitization, sustainability, and energy-saving plans are accelerating automation projects in many companies. Once manual processes that lend themselves to automation have been identified, the next question that usually follows is: And what does it all cost?It can make sense to consider options such as leasing or robot-as-a-service. One example of tools that give small and medium-sized enterprises (SMEs) in particular a better overview the financial aspects of automation is the ROI calculator from OMRON. Anyone currently considering the purchase of a cobot or AMR can use this tool to reveal the return on investment.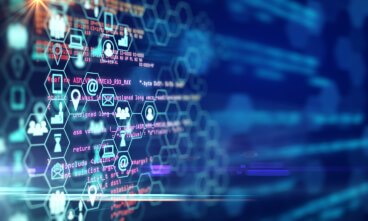
Complying with industry regulations
20 April, 2023 In the second blog in this series on Traceability we will discover how complying with industry regulations is essential in today’s manufacturing process, especially in industries like food, beverage and pharmaceutical and what the legal requirements are set out by the FSA.A lack of a comprehensive traceability system can potentially have disastrous outcomes for everyone in the supply chain, from producer to consumer. Paper does not control anything. It is just a written record, there’s no validation, and no control.In the food and beverage industry, authenticity is essential. Consumers need to know that the foods they are purchasing consist of the things listed on their labels, as food allergies and expired foods can cause serious illness and possibly death. Since both public health and consumer satisfaction depend so heavily on product integrity, the food and beverage packaging industry is highly regulated.One of the main things mandated by food and beverage regulation is “traceability” the practice of maintaining thorough records on the origins and whereabouts of products and raw materials by scanning printed barcodes, direct part marks (DPMs) or radio frequency identification (RFID) tags throughout the production process and the supply chain. From raw materials supplier to production line to supermarket to customer, the creation and distribution of a particular food item should be as transparent as possible.Food and beverage manufacturers also benefit directly from traceability protocols that minimise the occurrence and effect of costly issues such as product recalls by providing real-time data on supplier materials, processes and machinery involved in production. These protocols can significantly reduce cost of a recall by isolating tainted items and making it unnecessary to pull large amounts of non-tainted product off the shelves.Regulations are one of the primary forces spurring food and beverage manufacturers to adopt robust traceability systems. In the United Kingdom, the foremost source of regulation is the Food Standards Agency.After a number of high-profile outbreaks of food related illnesses in 2000, the Food Standards Agency (FSA) was established as an independent government department working to protect public health and consumers’ wider interests in relation to food in England, Wales and Northern Ireland.In the wake of Brexit, food and beverage regulations in the United Kingdom have changed and evolved while retaining some relevant provisions laid out in EU legislation. While Northern Ireland remains subject to EU law alone, Great Britain, Wales and Scotland fall under the provision of the Food Standards Agency (FSA) as the government organisation responsible for setting and enforcing traceability requirements.A quick reference guide published by FSA specifies that food business operators (FBOs) must maintain traceability information for suppliers and customers—equivalent to the “one step forward, one step backward” model which means they must be able to identify the businesses to which their products have been supplied and to trace food chain inputs back to the immediate supplier.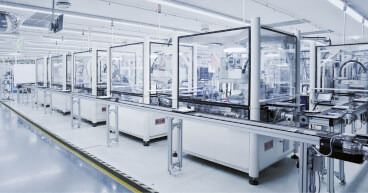
3 Reasons Leasing De-Risks Investments in Robotics
17 April, 2023 With skyrocketing energy bills, supply chain chaos, high interest rates, staff shortages, and the cost of living crisis reducing consumer demand, UK businesses feel like they are being hit from all sides at the moment.The economic outlook is challenging. Rising costs are squeezing profit margins forcing companies to charge higher prices or reduce output. In fact, the UK economy is the only G7 member yet to rebound to its pre-pandemic size. Industries struggling include manufacturing, which shrank by 4% in 2022 and is expected to decline another 3.2% in 2023, and logistics, which saw low levels of new warehousing space requirements at the end of last year. Companies looking to upgrade or expand are being held back by difficult economic conditions, in particular higher borrowing costs. When credit is cheap and readily available, businesses can make significant capital expenditure (capex) investments, transforming their operations to reduce costs in the long run or increase output and boost revenue. For manufacturing and logistics companies, high interest rates reduce the viability of investing in new technologies such as collaborative robots (cobots) and autonomous mobile robots (AMRs). In competitive industries where productivity is key, this puts many operations at risk of falling behind the competition. Thankfully, there is another option available. OMRON offers leasing options to help businesses acquire market-leading equipment without the risks associated with capex investments during tough economic times. Leasing advanced robotic equipment provides critical financial and operational benefits for companies looking to upgrade their operations.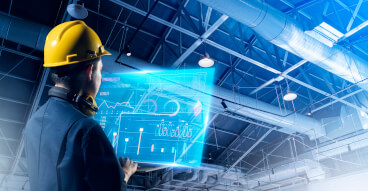
4 Steps to Optimise Manufacturing Operations Using Production Data
17 April, 2023 Bottlenecks and other production issues are the scourge of efficiency, costing businesses thousands, if not millions, a year through delays, disruptions, wasted resources, and lost output. Based on your assets (staff, equipment, facilities, etc.), what should your business be capable of producing? Most businesses have at least done a back of an envelope calculation on what their optimum output could be, if not taken the time to do a detailed analysis breaking down every process in the production chain. How far off is your actual throughput compared to the best-case scenario? In highly competitive markets with shrinking margins and a challenging economic forecast, businesses have to find ways to maximise their operations, getting as close as possible to optimal performance. They can no longer accept inefficient processes such as:Unbalanced assembly linesLong changeover timesMinor discrepancies compounding to increase the failure ratePoor equipment efficiency or extended maintenance downtimeUntrained staff slowing productionThankfully, manufacturing has come a long way. With the integration of new technologies (robotics, IoT, AI, etc.), companies can generate and track considerable production data. However, having data is just the start. To impact your operations for the better, businesses must derive actionable insights from it. Listed below are four steps to help businesses identify and resolve production issues.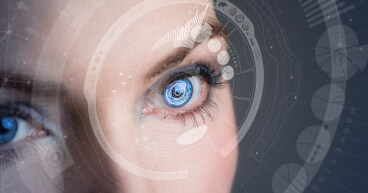
Traceability
13 April, 2023 During this series of blogs focusing on Traceability we will discover how traceability in manufacturing has evolved over time from its first iteration to today’s evolution Traceability 4.0.Traceability definitions have been evolving since the invention of automatic data capture equipment – primarily barcode readers – over 40 years ago. Since then, traceability applications have evolved to support industrial development from both a product technology and business process perspective.The breadth and scope of traceability has expanded significantly over the years along with advances in technology, making it a critical application for today’s world-class manufacturers. In this post will explore the evolution of traceability and explain why the latest phase, Traceability 4.0, is not just about tracking products throughout the supply chain but also optimising productivity, quality and brand reputation within the manufacturing operation by tying product to process parameters.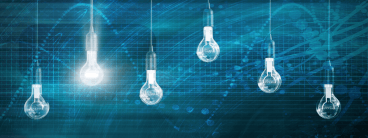
Accelerating socially driven innovation
28 March, 2023 Society is built on cultural norms and values that shape how people think, behave, and interact with each other. These cultural factors can influence everything from consumer preferences and business practices to political beliefs, which in turn affect how manufacturing evolves.Manufacturing is one of the most important sectors of any economy, yet in the UK it can fairly claim to be underrated - despite our being the world’s 9th largest manufacturing nation. According to MAKE UK research, manufacturing provides 2.7 million jobs, has an annual output of £191 billion, and offers wages 13% higher, on average, than the rest of the economy.The sector also has a multiplier effect which extends far beyond the jobs and wealth it creates directly, supporting the growth of other industries and creating a positive cycle of economic growth - boosting the overall productivity of the country and improving lives.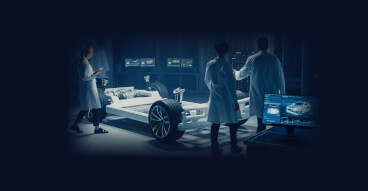
Why automated inspection systems are critical for electric vehicle manufacturing
23 March, 2023 Safety trumps all other concerns in the automotive industry, and electric vehicle manufacturing is no exception. However, safety can also introduce complexity, and the complexity of today’s vehicles – particularly EVs – is such that manufacturers are no longer able to rely on traditional sample or audit-based inspection methods.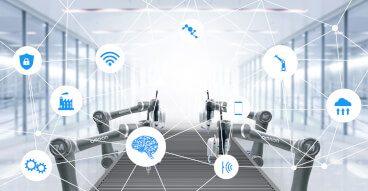
Can Artificial Intelligence (AI) in robot systems manage the functional safety parts?
20 March, 2023 Authors: Josep Plassa, Safety Product Marketing Manager at OMRON Europe and Atsushi Oshiro, Manager at the OMRON Development CenterRobots and AI systems have become an integral part of industrial manufacturing sites. To ensure the safety of workers while using robots, a detailed risk assessment is necessary. This assessment is carried out from the perspective of Functional Safety, which examines the five main elements employed by robots to determine autonomous control actions: Environment recognition, Action planning, Trajectory generation, Motion control, and Measurement.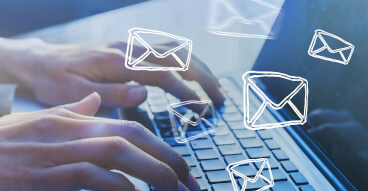
How Remote Connectivity can help your company through challenging economic times
27 February, 2023 What was supposed to be a period of recovery for the manufacturing industry post-pandemic has turned into anything but. Labour shortages persist, except now they’re compounded by high inflation, a looming recession, the conflict in Ukraine, and political mayhem at home. It can feel like every day brings another challenge to overcome. UK manufacturing was already at an inflection point, with businesses looking to transform their operations, introduce new technologies, and find ways to increase automation. Unfortunately, this can require an injection of capital that is harder to find at a time of financial uncertainty.As we round out 2022 with our third government of the year, we are still not sure how the new premiership of Rishi Sunak plans to solve the black hole that is the nation’s finances. But one thing is for certain, costs will rise, and UK manufacturing has a tumultuous road ahead. However, even when market conditions are tough, opportunities remain. In this blog, we will discuss the challenges of investing in new machinery, particularly given the economic outlook and how remote connectivity can help maximise its use while also minimising operational costs.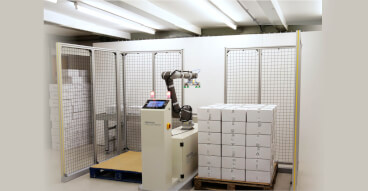
How the RB1200 Cobot Palletiser can transform your businesses’ labelling needs
17 September, 2021 For many businesses, the logistics of transferring large amounts of inventory around their facility is a significant headache. Everything has to be labelled and organised to ensure it gets sent to the correct location for use, storage, or shipping. Even minor errors during the labelling process reduce efficiency and can potentially compound to create costly mistakes. The job itself is not a desirable one, though. Human beings are not best suited for repetitive tasks whilst staying alert and maintaining concentration to ensure mistakes don’t occur. This is, however, a task tailor-made for automation.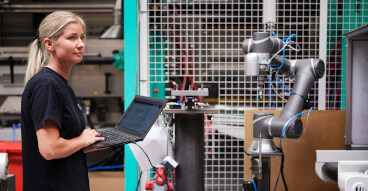
Unika makes Landmark decision to bring quality levels to new heights
25 August, 2021 OMRON TM cobots with integrated vision system eliminate human error, increase production efficiency.
Flexible, safe and easy collaborative welding solution from Guidetti Technology
20 August, 2021 Guidetti Technology SRL has integrated OMRON collaborative robots (cobots) into its ‘EasyArc’ welding solution. This is used in collaborative applications on small batches of various types of metal carpentry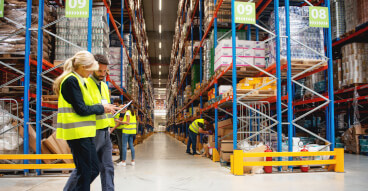
How labour shortages are affecting the logistics sector and why automation is the solution
11 August, 2021 By Stuart Coulton, Regional Manager, OMRON UK North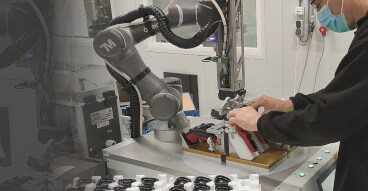
Professional help for personal care: Putting a cobot to work
09 July, 2021 Of the many processes involved in finalising a consumer product, the final step can often be the most intricate. For this OMRON customer, the last step in production is to fasten the cover holding screw, closing up the unit—in this case, an electric shaver. Traditionally, the full process was completed manually, with an electric screwdriver in a multi-step process. This repetitive task is an ideal candidate for the help of an OMRON cobot.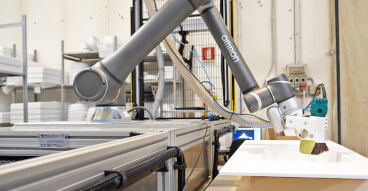
Cobot boosts production by 15% at Topcustom
23 June, 2021 Topcustom srl, an Italian producer of custom-made bathroom sinks, has recently transformed part of its operations by deploying a collaborative robot (cobot) from OMRON. The new cobot is being used to automate all the finishing operations of Topcustom’s products made from Ocritech. This is a light material that is easy to work, guarantees perfect hygiene and has excellent resistance to UV rays.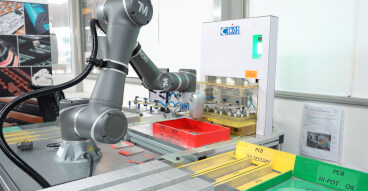
Cisel ensures traceability, safety and quality by testing printed circuit boards with a cobot
17 June, 2021 Cisel is an Italian company that specialises in the design and production of flexible printed circuit boards (PCBs) for the automotive, civil engineering and manufacturing industries. The company recently chose an OMRON TM5 collaborative robot (cobot) to automate the electrical testing of boards used in the power steering system of a leading automotive manufacturer.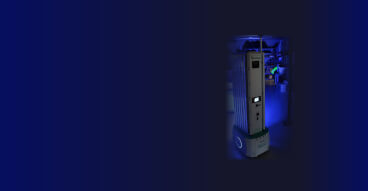
UV-C Robot helps businesses win the fight against Covid
16 June, 2021 As the UK’s customer-facing businesses plan their reopening strategies, keeping consumers and staff safe from Covid will be a key priority. In a bid to prevent future outbreaks at high footfall, everyday environments like supermarkets, bars and gyms, we have teamed up with UV Systems UK to produce an autonomous robotic sterilisation system that guarantees to kill the virus without damage or harm to surrounding goods.
Cobot ensures precise assembly of magnets for LITMAT’s drain plugs
03 June, 2021 Collaborative robots (cobots) are being used more and more extensively, in a range of different industries and across a wide variety of applications. They can make a significant difference to the efficiency and productivity of the production cycle. One company that is enjoying such benefits is LITMAT SpA.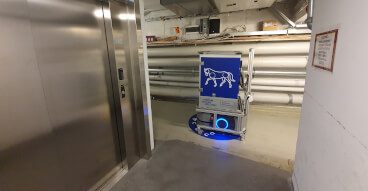
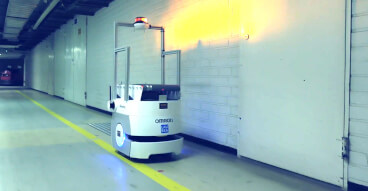
Mobile robot transports waste for Kymenlaakso Central Hospital in Finland
07 April, 2021 Waste transportation and logistics planning require a lot of work in hospital environments. Waste shipment is also a physical task that places demands on both time and human resources.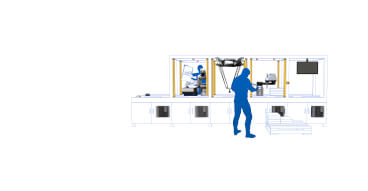
Choosing a robot for a smart factory
02 April, 2021 Anyone planning to move towards a smart factory needs to choose carefully when considering possible robotic solutions. Should it be an industrial robot or a collaborative robot (cobot)? Autonomous mobile robot (AMR) technology or a fixed selective compliance assembly robot arm (SCARA)? The answer will depend on your specific needs.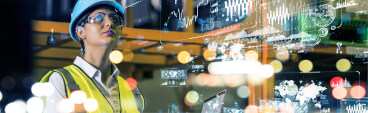
Data paradise factory floor: get more out of your machine and production information
25 September, 2020 Strategic Data Science is an essential pillar of every Industry 4.0 scenario. A four-step data mining approach based on CRISP-DM supports successful projects.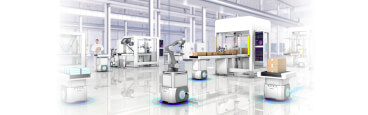
Get the full value from your factory floor data with data sciences
19 June, 2020 Industry 4.0 and IIoT have been buzz words for several years and these concepts are actually implemented on more and more machines. A huge amount of data becomes available: machine data, data of the production process and data regarding the manufactured product. Big Data has entered the factory floor.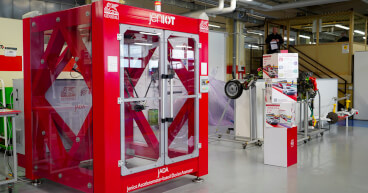
High-speed robot tests the reliability of black boxes
14 May, 2020 A non-destructive alternative to crash tests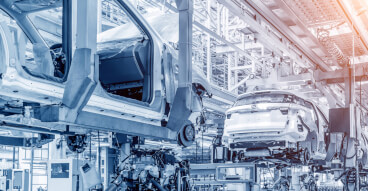
Integrated data control, motion control and machine vision for next-generation automotive production line
24 April, 2020 The Mexican regional headquarters of a leading manufacturer of premium air brake actuators for global on-highway and specialty markets required a new automated production assembly line. One of the company’s key performance indicators is to deliver a fully assembled product every 30 seconds, and it is with this end goal at the forefront that the team started the process of automating the production line.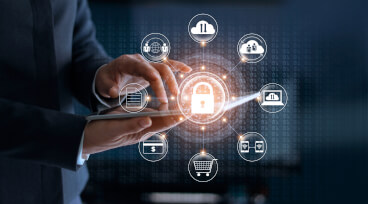
IoT security for manufacturers
11 December, 2019 The Internet of Things (IoT) is a recent concept, involving the connection of devices that incorporate electronics, software or sensors, with the aim of collecting and exchanging data.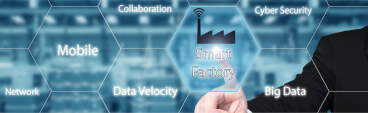
Smart machines: laying the golden egg?
16 October, 2019 Greater manufacturing efficiency: it’s the golden egg we’re all looking for. But it’s getting increasingly hard to find. The solution could be smarter automation, which involves lots and lots of data (‘big data’) and data collection and data-driven modelling. The smart machine then uses the models to automatically adjust its own behaviour (i.e. machine learning).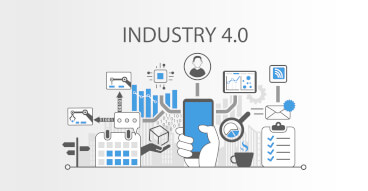
A practical illustration of IoT and Industry 4.0
01 October, 2019 The Internet of Things (IoT) is a relatively new phenomenon. Prof Dr Thomas Pospiech, a teacher of Production and Process Management at Heilbronn University of Applied Sciences, was interviewed recently about the ‘IoT box’ he’s developed to give his students a practical illustration of this fairly abstract concept.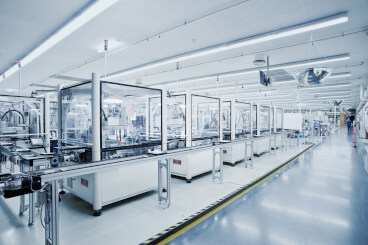
What is the effect of Brexit on automation in the UK?
26 September, 2019 Currently, workers from the EU have the right to travel and work freely across European borders. However, key statistics of net migration from the Office of National Statistics in the UK, show that net migration to the UK has been significantly reduced since 2016. With the announcement of Brexit, and the ensuing uncertainty around it, UK factories are perhaps no longer a viable destination for European workers.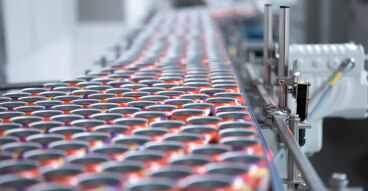
How smart is your packaging line?
17 September, 2019 Industry 4.0 is changing the way in which manufactured goods are produced, through the use of automation and data exchange. By incorporating it into your packaging line, you can start to enjoy a range of benefits, from better data management to improved efficiency. Moving to a modern, flexible and smart line will bring the most benefits, but replacing a complete production line might not be a viable option if you’re operating with tight margins. However, even small changes to your existing facilities can significantly boost your efficiency.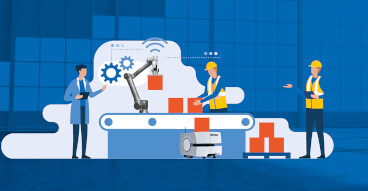
Four top tips for automation projects in the food and beverage industry
22 February, 2021 A challenge accelerated by the Coronavirus pandemic has seen producers having to juggle between longer term range proliferation centred on consumer demands, and range (SKU’s) reduction caused by retailers and consumers rapidly changing buying habits. Companies that break new ground by using innovative technologies not only gain agility but also reduce scrap, contamination risk, waste and losses.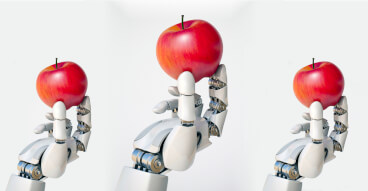
Factory automation: four tips for the future of food & beverage manufacturing
16 July, 2020 The coronavirus pandemic has posed major challenges to organisations of all types and sizes. In the food and commodity industry, companies have faced significantly reduced consumption and disrupted supply chains, while at-home consumption increased, and out-of-home consumption came near to a standstill. But how can manufacturers adapt their business strategies and production processes both now and in the longer term? The pandemic may provide an opportunity for rethinking outdated processes and procedures and enhancing them with concepts such as innovative robotics, sensor technology and holistic automation strategies.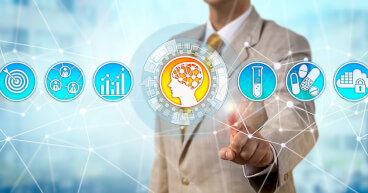
Improve OEE with Artificial Intelligence at the Edge in Food Manufacturing
16 October, 2019 Implementation of Artificial Intelligence (AI) in food manufacturing is picking up speed. Many F&B companies are realizing that AI presents an opportunity to increase not only the Overall Equipment Effectiveness (OEE) – and therefore combine reduced costs with increased productivity – but also to improve the analysis of data to support continuous improvement programs such as reducing waste or process operations variability.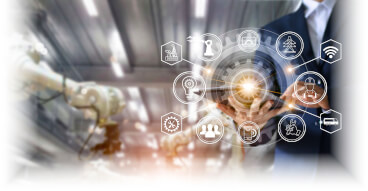
3 Steps to Optimize Operational Efficiency for the Future of Manufacturing
02 October, 2019 Operational Excellence is required to maximize capital expenditures. But at the same time manufacturers are challenged to move away from traditional high volume, low mix production runs, to more complex high mix, low volume production with consumer demand linked directly with production. How to optimize operational efficiency to be ready for the future of manufacturing?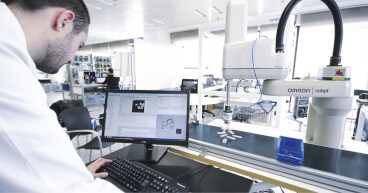
The power of collaboration between machines, people and teams
01 October, 2019 With today’s rapid advances in technology, the manufacturing sector needs to be increasingly agile, ready to adapt to changing demands. Production lines must be more flexible, so that they can cope with shorter production runs, more varied products and tight deadlines. So how can manufacturers address these challenges? The solution lies in more advanced, interconnected and intelligent systems that can be programmed to handle a range of tasks.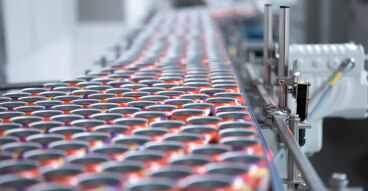
Minimum complexity, Maximum yield
08 July, 2019 Omron's leading position in packaging automation in the Food & Beverage industry is based on smart and simple solutions that result in solid success. A concept that we dubbed Perfect Packaging. Omron's Perfect Packaging approach structurally eliminates risks and boosts production even in tough situations when high throughput is required. But also optimises your filling. Minimising under- or overfill.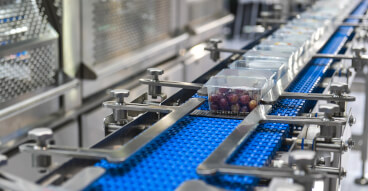
At Omron we serve to protect Package Integrity!
08 July, 2019 Protecting a product is the main purpose of any package. Food packaging that is not closed completely airtight can cause a whole range of problems resulting in huge expenses and problematic long-term consequences for manufacturers. Loss of nutrients and aroma to premature spoilage are the least problematic relative to the costly aftermath that easily comes around the corner when consumer health is at stake and recalls enter the media.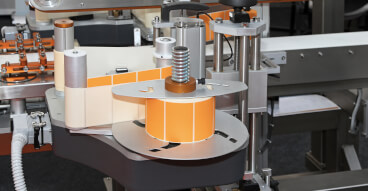
Perfect Packaging, ordinary packaging executed extraordinary well
08 July, 2019 Packaging processes rarely harbour extremely surprising variables. From manufacturers to system integrators, machine builders and industrial automation providers, we all know the essentials that make packaging production a definite success. However, the everyday reality on the factory floor is that small imperfections in the process result in major output disturbances. That is why Omron introduces its Perfect Packaging concept featuring smart innovations that ensure that ordinary F&B-packaging is executed extraordinary well. We help make your bottom-line top!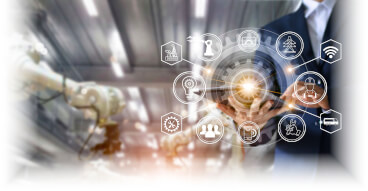
Go with the Adaptive and Dynamic production flow!
06 May, 2019 Flexible and fast responses to changes in market dynamics improve performance. Made-for-me production flows are the future of manufacturing coherent with Industry 4.0. A reality that Omron already provides today through its cutting edge innovative-Automation approach. Turning factory floor data into highly valuable information, we realize intelligent automation solutions for manufacturers around the globe.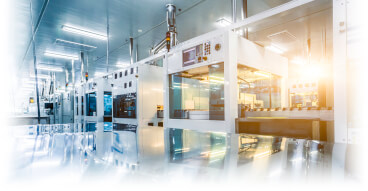
Smart sensing for multiple materials!
06 May, 2019 You know the routine. Switching from one product to another on your production line means a costly full stop, making all kinds of changes, starting up again, discarding the materials and packaging already fed into the line together with start-up rejects, and only then can production resume. Well, have we got good news for you: smart sensing for multiple materials!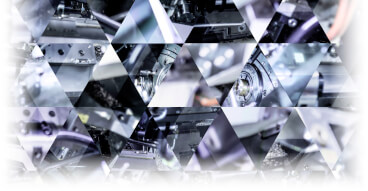
Rock solid results with flexible production & robotics!
06 May, 2019 Today's market requires an increasingly agile production environment. Traditional industrial automation and robots are often too inflexible to successfully accomplish mass customization. Omron is enabling smart Industry 4.0 scenarios with a rare combination of intelligent automation solutions and robotics. Perfecting seamless human-robot collaboration and making more and more use of AI-driven possibilities, we assist manufacturers in realizing rock solid results with flexible production and robotics.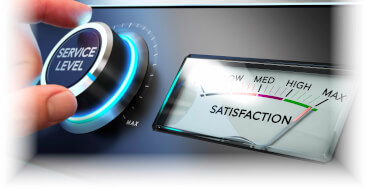