Automation blog
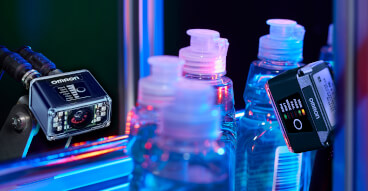
Revolutionising Quality Control: AI and Data Capture Transform Manufacturing
12 March, 2025 Maintaining consistent product quality in modern manufacturing can feel like a relentless challenge. Just as one issue is resolved, another arises to test your processes to their limits. Whether you're a production manager keeping the assembly line efficient, an engineer integrating new technologies, a salesperson offering innovative solutions, or a machine builder designing the next generation of equipment, product defects are a common hurdle.But what if there was a way to significantly reduce these defects, meet regulatory requirements with ease, and enhance overall business performance? Next generation technologies leveraging Artificial Intelligence (AI) and advanced product data capture may be the solutions you need.Specifically, we are referring to four cutting-edge technologies making a significant impact on quality control: Automated Traceability: Monitoring every product's journey through data capture. AI Vision Systems: Enhancing inspection beyond human capabilities. Digital Watermarking: Protecting product integrity through embedded data. AI-Driven Sealing Solutions: Perfecting packaging with intelligent adjustments. In this blog, we’ll explore how these technologies can help you achieve excellence in quality control, no matter your role in the manufacturing sector.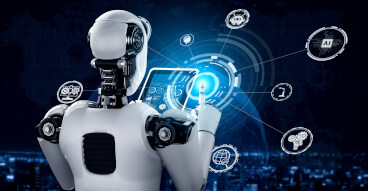
Optimising Production: How Smart Maintenance Technologies Are Changing the Game
21 January, 2025 Unplanned downtime is sabotaging production goals. It's time to take action.Unexpected machine stoppages aren't just inconveniences—they represent costly disruptions that derail schedules, increase operational expenses, and reduce profitability. Efficiency and reliability are crucial factors for maintaining competitiveness in manufacturing, so, minimising productivity losses such as unplanned downtime must be a strategic priority for both small and medium enterprises (SMEs) and large corporations.But what if you could anticipate equipment failures before they happen, deploy machines designed with maintenance in mind, and minimise fault finding? Smart maintenance technologies are making all of these a reality, transforming operations from reactive firefighting to proactive problem-solving.In this blog, we’ll explore how predictive maintenance, intelligent machine design, and advanced diagnostics are helping manufacturers reduce downtime, optimise costs, and stay ahead in an ever-evolving industry.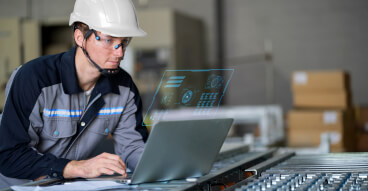
Navigating the new machinery directive
16 January, 2025 The European Union’s transition from the 2006/42/EC Machinery Directive to the new Machinery Regulation (2023/1230/EU), effective January 20, 2027, represents a significant shift in legislative requirements for machinery and related products. For system integrators, the regulation introduces stricter requirements for the incorporation of AI-driven systems, autonomous machines, and interconnected equipment. For end users, especially those operating complex machinery systems, preparing for these changes is a strategic necessity.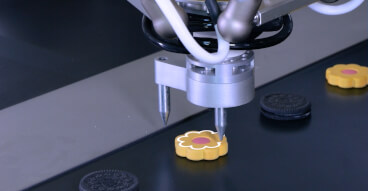
Creating smarter, faster, and simpler multi-robot packaging lines?
16 January, 2025 Does integrating robotics into a packaging line feel like solving a puzzle with too many pieces? Designing a high-performing packaging line with multiple robots often involves navigating complex integrations, precise motion control, and the need to meet tight production demands. Whether you are a System Integrator crafting tailored solutions for specific client needs or an OEM developing scalable, standardized systems, the OMRON Robotics Packaging Library provides the tools to simplify integration and reduce engineering time. Here’s how the Robotics Packaging Library helps you improve performance and reduce complexity in packaging automation.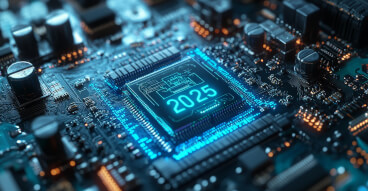
From optimization to autonomy - Top five manufacturing automation trends for 2025 from OMRON
04 January, 2025 As we step into 2025, the world of industrial automation is approaching a new chapter. According to OMRON's SINIC Theory, which ties technological advances to societal change, we’re now moving from the Optimization Society to the Autonomous Society. The theory, created in 1970 by OMRON’s founder Kazuma Tateishi, predicts future societal and technological developments to guide innovation. In the Optimization phase, the focus has been on refining processes, boosting efficiency, and using technology to improve operations. But the Autonomous Society is a whole new era—one where systems don’t just run efficiently; they become self-regulating, self-learning, and capable of independent decision-making.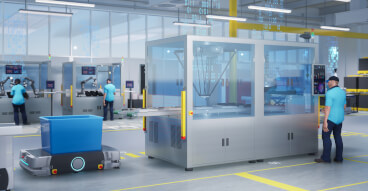
Securing a battery-powered future through automated recycling
17 December, 2024 Batteries have a crucial role to play in facilitating the scaling up of renewables in the power mix and the electrification of transport, as we transition away from fossil fuel dependence and towards cleaner energy technologies to meet the targets agreed at COP 28.This has sent the battery market on an upwards trajectory, with two sectors - power and transport - driving demand. According to the International Energy Agency (IEA), the energy sector accounts for over 90% of overall battery demand. It reported that in 2023 alone, battery deployment in this sector increased by more than 130% year-on-year, adding a total of 42 gigawatts (GW) to electricity systems around the world. Energy storage is emerging as a major application for batteries as a means of capturing renewable energy and is only going to become more important in the future. In the transport sector, meanwhile, batteries have facilitated the rise of electric cars, bikes, trucks, buses and other battery-powered vehicles.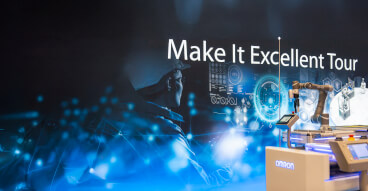
Beyond tech for tech’s sake: What happens when industrial automation meets operational excellence
30 November, 2024 The past few years have seen rapid technological advancements, with the rise of AI standing out as a key trend. In a survey of manufacturers across the UK, US, and Canada, 70% said they had implemented some form of AI into their operations. This willingness to embrace new technologies is impressive, especially since manufacturing industries have so much to gain from automation.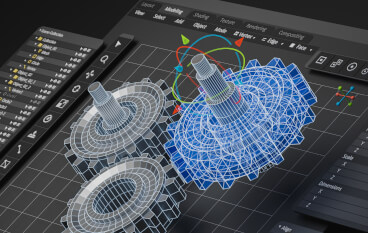
Taking the first steps to successful digitalisation
12 November, 2024 Building a digital factory isn’t an end or a reason in itself. A digital factory is a tool that gives manufacturing businesses the flexibility to respond to changes in the market - whether that is innovation trends or cost increases, and whether they are operating in the food & beverage, personal care, pharmaceutical or automotive sector.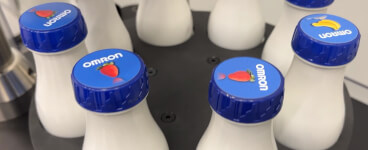
PPWR: why cross-chain collaboration, traceability and smart packaging are key
24 September, 2024 According to Eurostat figures, in 2021, each person living in the EU generated 188.7 kg packaging - almost 32 kg more than in 2011. Over this period, the amount of plastic packaging waste increased by 27%. Whilst recycling rates have also increased, a large volume of plastic packaging is still not being recycled - the latest statistics suggest that only a handful of countries in Europe are achieving a 50% recycling rate for plastics. Recognising that the existing legal framework was failing to drive improvement in packaging waste reduction, in 2022 the Commission proposed a revision to the 2018 directive for Packaging and Packaging Waste Regulation (PPWR).The revised PPWR is expected to enter into force by end of this year, and will fundamentally change the way packaging is designed, consumed and disposed of. The updated regulation is broad in its scope, but the underlying aims are to reduce the amount of packaging waste generated and increase packaging recyclability.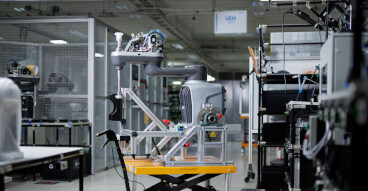
Avoiding efficiency blockage: Why companies should not postpone their robotics plans?
24 September, 2024 Delaying investments in innovative technologies is associated with numerous risks. Companies that are still hesitant should ask themselves three questions.The European economy faces a range of challenges that impact its growth, stability, and competitiveness. Europe, for example, has one of the oldest populations in the world. An aging workforce increases the burden on social security systems and reduces the labor supply, potentially slowing economic growth. Furthermore, the EU's commitment to the Green Deal and achieving carbon neutrality by 2050 requires substantial investments and structural changes in various sectors. Added to this is a lack of willingness to invest due to financial worries. A recent study by the McKinsey Global Institute (MGI) found that large European firms with more than $1 billion in revenue have fallen behind their US counterparts. They collectively invest $400 billion a year less and grow one-third more slowly.This investment fatigue can lead to several problems that have both short- and long-term effects, including disadvantages in terms of competitiveness, sustainability, and reputation, lower productivity, and less success in attracting new skilled workers. Innovative robotics can counteract such developments but also requires well-thought-out financing. Therefore, companies that are currently limiting their investments should urgently ask themselves whether this will not have more negative consequences for them in the long term than short-term savings. The following three questions should be the focus of such considerations: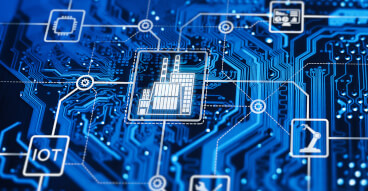
Digitising with open standards: the recipe for a good night’s sleep
02 September, 2024 Can we commit to the predictions I have made? Will we be able to deliver to the deadline? Do I have enough insight to know for sure? How is the factory doing in terms of QCDE (quality, cost, delivery time and environmental impact) against our targets and compared to the competition? These are some of the concerns that keep factory managers awake at night; concerns that can be addressed through digitisation. In a digitised production environment, factory managers don’t have to worry about the unknowns, the risks and the might-happens. Digitisation eliminates uncertainty and enables performance-driven optimisation. It provides insights that can help factory managers improve quality, reduce cost, shorten lead times and reduce environmental impact. The manager of a digitised factory shouldn’t wake up worrying in the middle of the night, but if they do, a brief glance at their mobile phone should reassure them that everything is running as it should be. However, moving from a state of anxiety-induced insomnia to one of blissful somnolence is not easy. Put bluntly, digitisation can be quite tedious. Project leaders rarely have the luxury of working with a blank canvas; most of the time they are working with a patchwork quilt of old technologies sewn together; they are trying to digitise production lines incorporating machines that have never logged data and were built before data communication protocols even existed. This all adds up to a sizeable OT and IT integration challenge.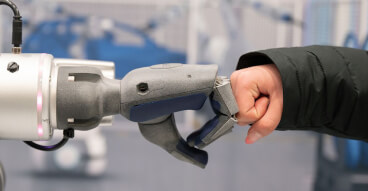
Robotic Trends 2024: Simple and flexible application essential to reach full potential
15 July, 2024 From load carrier to colleague to team player: the role of robots has changed dramatically over the past seven decades. AI is creating more possibilities, but humans remain the determining factor. Robots or humans – who will determine production in the future? Since George Devol's 1954 patent for a programmable manipulator, this question has sparked debate. Devol's Unimate robot revolutionized industry by safely performing dangerous tasks, highlighting that the focus isn't robots vs. humans but rather "robot + human = efficiency." Over 70 years, industry demands have evolved to prioritize flexibility, scalability, adaptability, and sustainability. Robots handle tasks that free humans to focus on value-added activities.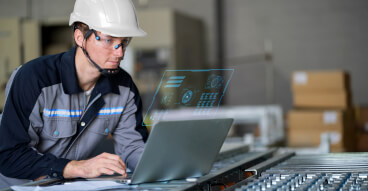
Navigating the new machinery directive
16 January, 2025 The European Union’s transition from the 2006/42/EC Machinery Directive to the new Machinery Regulation (2023/1230/EU), effective January 20, 2027, represents a significant shift in legislative requirements for machinery and related products. For system integrators, the regulation introduces stricter requirements for the incorporation of AI-driven systems, autonomous machines, and interconnected equipment. For end users, especially those operating complex machinery systems, preparing for these changes is a strategic necessity.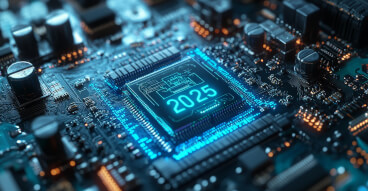
From optimization to autonomy - Top five manufacturing automation trends for 2025 from OMRON
04 January, 2025 As we step into 2025, the world of industrial automation is approaching a new chapter. According to OMRON's SINIC Theory, which ties technological advances to societal change, we’re now moving from the Optimization Society to the Autonomous Society. The theory, created in 1970 by OMRON’s founder Kazuma Tateishi, predicts future societal and technological developments to guide innovation. In the Optimization phase, the focus has been on refining processes, boosting efficiency, and using technology to improve operations. But the Autonomous Society is a whole new era—one where systems don’t just run efficiently; they become self-regulating, self-learning, and capable of independent decision-making.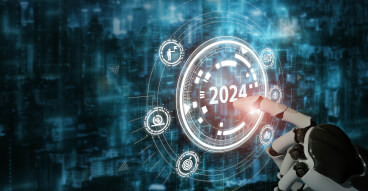
What’s in store for automation in 2024? Six predictions from OMRON Europe
13 December, 2023 The succession of shocks over the last few years has heralded a new era of heightened geopolitical and economic risk. This is prompting manufacturers to build resilience and flexibility into business models and rethink global supply chains and relationships. At the same time, pressure is mounting to incorporate ESG principles into operational decision making. AI, data science, digital twins and sensing, monitoring and vision technology will all be essential to developing automation and control solutions that can help the manufacturing industry adapt to this new reality. In this context, I would like to share the top six trends that will impact and shape industrial automation in 2024 and beyond.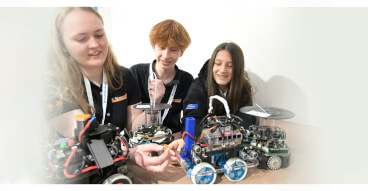
Empowering the workforce: OMRON's approach to skills development in European manufacturing
06 September, 2023 Delving into OMRON's unwavering commitment to nurturing skills that empower the next generation, while the industry embarks on a transformative journey – a journey that unlocks the full potential of the Fourth Industrial Revolution (4IR) while boldly moving towards the Fifth Industrial Revolution (5IR).In the halls of academia, the boardrooms of visionary business leaders, and the chambers of forward-thinking politicians, a fervent debate evokes. It revolves around the profound shift from the Fourth Industrial Revolution, 4IR, or Industry 4.0 as it is also known, to Industry 5.0 will change the world in which we live.Historically the Industrial Revolution was the First Machine Age, and electricity the Second, then electronics was the Third, and the internet as platform the Fourth Machine Age. We are now entering the Fifth Machine Age, which highlights harmonious human-machine collaboration and the contributions of the industry to society. This is the moment to not only adapt but to lead, to pioneer, and to create a future where innovation knows no bounds. Klaus Schwab, the founder and executive chairman of the World Economic Forum has observed that: “We stand on the brink of a technological revolution that will fundamentally alter the way we live, work, and relate to one another. In its scale, scope, and complexity, the transformation will be unlike anything humankind has experienced before. Our world is undergoing a transformative shift. Global production is evolving, driven by the automation of traditional industrial practices through smart technology, M2M communication, and IoT integration. This synergy fuels heightened automation, seamless communication, and intelligent machines that autonomously analyse and diagnose challenges.The rise of AI sparks debates, hinting at deeper transformations within our societal tapestry. As we navigate this dynamic landscape, we are poised to embrace innovation and reshape our future.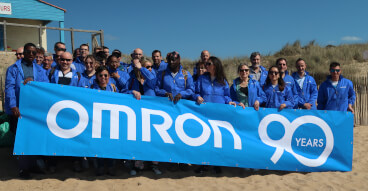
From red lights to robots: OMRON celebrates 90 years of innovation
06 June, 2023 This year on Founder’s Day, OMRON looked back on 90 years of pushing technological boundaries, and looks forward to a future of automation innovation framed by sustainability, digitalisation and human-machine collaboration.May the 10th be with you… Every year, 10th May is probably the most important day in OMRON’s calendar. On this day, 30,000 OMRON employees around the world celebrate the life and legacy of the company’s founder, Kazuma Tateishi. They do this by recommitting to Tateishi’s vision of using technology to create a better world and by giving back to society - often by participating in volunteer and charity projects in their communities. Innovation Milestones OMRON's journey of innovation began in 1933 with the development of a high-precision timer for X-ray photography. This marked the company's first contribution to addressing societal needs. In 1960, OMRON unveiled the world's first non-contact proximity switch, revolutionizing advanced mass production capabilities. Since then, OMRON has continued to introduce groundbreaking technologies, including the first automatic traffic signal, unmanned train station system, wearable blood pressure controller, ultra-high-speed fuzzy logical controller, and automatic cancer cell diagnostic equipment.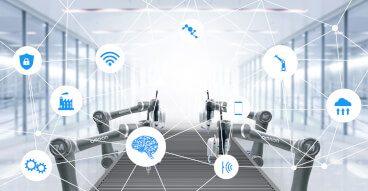
Can Artificial Intelligence (AI) in robot systems manage the functional safety parts?
20 March, 2023 Authors: Josep Plassa, Safety Product Marketing Manager at OMRON Europe and Atsushi Oshiro, Manager at the OMRON Development CenterRobots and AI systems have become an integral part of industrial manufacturing sites. To ensure the safety of workers while using robots, a detailed risk assessment is necessary. This assessment is carried out from the perspective of Functional Safety, which examines the five main elements employed by robots to determine autonomous control actions: Environment recognition, Action planning, Trajectory generation, Motion control, and Measurement.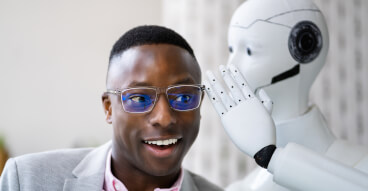
Artificial Intelligence: don’t call me stupid
08 February, 2023 Ten years ago I was quite proud of how smart the machines in our own factory were. Now, with my today’s definition of smart, I realise they were actually quite stupid.Why? Because although they were doing what they were designed to do, the minute they encountered anything unexpected or out of the ordinary they were stumped. They resorted to asking the operator ‘what is wrong with me?’.Troubleshooting and getting machines back up and running called for smart people. Highly skilled operators. Experienced software and hardware engineers. The problem is that in the last ten years, these people have become increasingly unavailable. There quite simply isn’t enough new talent entering the industry to offset the number of workers reaching retirement age. When they leave the business, retirees take with them their hard-earned on-the-job knowledge that is a culmination of years of experience. With each departing worker, businesses are faced with the prospect of a less productive and less skilled workforce.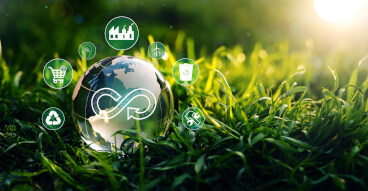
The path to net zero: talking tactics
01 February, 2023 The key to unlocking a net zero future in manufacturing is transforming the value chain through automation.In June 2022, New Scientist reported that a third of the world’s largest companies had net zero targets - significantly more than the same time last year.Whilst it is positive news that momentum is accelerating, the article went on to say that the details of how companies were planning to reach net zero were patchy.Which is not surprising really. Creating and implementing a net zero strategy is a huge undertaking for any business, especially with 80% of GHG emissions falling into Scope 3 - that is emissions that occur upstream or downstream in the value chain. This is a particular challenge for FMCG companies, whose supply chains and onward logistics are long and complex.Most of these businesses know what they need to do: decarbonise and circularise the value chain. And they have a strategy for doing this, which will generally cover: optimising the use of resources and energy, replacing high emission products and processes and eliminating waste.But translating intention into action is where the main challenge lies. This is where automation has a crucial role to play.Data collection and analysis is the key to successful net zero transition. Without it, how do companies know what their starting point is, where they need to improve, whether they have improved and by how much? Robust data is the foundation for turning a commitment into change, and for credibly and confidently communicating with stakeholders and delivering on climate ambitions.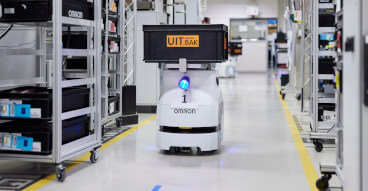
Powering through the energy and fuel crisis with automation
07 December, 2022 To counter rising prices and meet environmental targets, industrial enterprises should explore how automation technologies from a single source might help contribute to their sustainability strategy.High energy and fuel prices are putting a strain on both households and industry. Not only is the situation negatively impacting financial plans and wallets, but the excessive prices are forcing some companies to cease production. According to Make UK 42% of manufacturers surveyed said that their electricity bills have increased by 100% in the past 12 months and 32% said that gas prices have increased by over 100% in the past year. A worrying 12% of manufacturers have already made job cuts as a direct result of increased energy bills.The war in Ukraine, Covid-19 pandemic, and gas pricing are only a few of the causes of the crisis, which impacts all sectors and has an impact on everything from power prices to supply chains. What should manufacturing companies consider now? Comprehensive automation strategies are essential for greater flexibility and energy efficiency. This includes innovative robotics paired with sensor and vision technology as well as artificial intelligence – AI at the Edge. In addition, real-time data from production plants can assist with detecting anomalies and improving overall equipment effectiveness (OEE).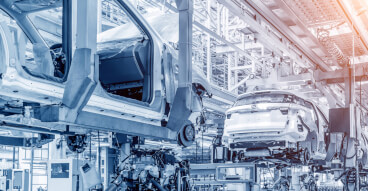
Where is the future heading, intralogistics? Tips for more efficiency
15 November, 2022 Sometimes we focus so much on the big picture that we forget the smaller and yet so important processes that characterize smart production. One example is intralogistics, i.e. the flows of materials and goods that take place on a company's premises or in a production hall. A recent study found that more than 80 percent of the companies surveyed consider the increased use of AI and automation in intralogistics to be necessary to meet challenges such as the shortage of skilled workers or growth plans.Automotive companies that want to meet market and customer requirements, increase efficiency and become more sustainable must come up with new ideas. Energy costs, the gas crisis, and rising inflation make this task even more difficult. Smart factory concepts that combine innovative automation, digitalization, and smart intralogistics approaches can provide valuable support. Some speak of Industry 4.0 in this context, others of the “factory of the future”, still others prefer Industrial Internet of Things (IIoT). But no matter which term you favor: The most important thing is to become active now and to rely on reliable partners. Intralogistics is a good starting point for quickly initiating change. Because action is urgently needed: many companies are currently severely limited due to the shortage of skilled workers. Modern technologies such as mobile robots can provide a remedy.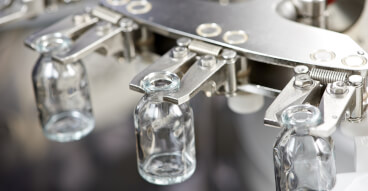
How can adaptive AI inspection contribute to flexible manufacturing?
04 October, 2022 Consumers today demand customized products to meet their personal needs and tastes. Instead of producing items that are ‘made to shelve’ and ‘sent to stock’, manufacturers must personalize products that are ‘made for me’ and ‘sent to me’. This is revolutionizing production and forcing companies to rethink their processes. At the same time, ensuring zero complaints and zero defects is a must.The trained eye of an experienced vision inspector is quick to spot errors, but a routine task like this is tiring, and cannot be carried out at each step of the production, especially due to the current labor shortages in many industries. But could this task be automated also in high-mix low-volume production? Could a smart vision system or an ‘electronic eye’ replicate the discernment of the human eye, with the added benefit of repeatability and robustness? The latest AI-enabled adaptive inspection can overcome the challenges of automated quality inspection, with improved flexibility, productivity, and adaptability.
Artificial Intelligence: hope, hype and FOMO
22 September, 2022 Ten years ago when we received enquiries about AI-based projects, they were mainly driven by hype or FOMO. When I asked why they wanted to get into AI, the answer, more often than not, was either ‘because my boss asked me to’, ‘because we have a lot of data’ or ‘because it seems like an interesting area’. None of these were particularly solid reasons and certainly didn’t justify the hefty investment that AI applications would have required at that time.That is changing, and hope, rather than hype or ‘FOMO’, is the driver. Customers don’t ask whether we can help them with AI anymore. They ask us whether we can help with predictive maintenance, quality control or process optimisation. They come to us with a problem that they want us to help solve. The adoption of AI is no longer a motive or an aim in itself. Instead, AI has become an ‘enabler’.Whatever the industry - whether food & drink, pharmaceutical, electronics or automotive - the end goal is the same: producing high quality, defect-free products at a lower cost, using less energy and less labour. And AI can be one of a suite of solutions for achieving those objectives.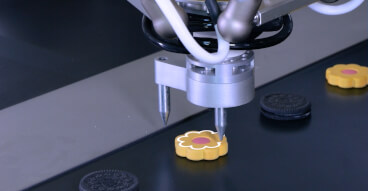
Creating smarter, faster, and simpler multi-robot packaging lines?
16 January, 2025 Does integrating robotics into a packaging line feel like solving a puzzle with too many pieces? Designing a high-performing packaging line with multiple robots often involves navigating complex integrations, precise motion control, and the need to meet tight production demands. Whether you are a System Integrator crafting tailored solutions for specific client needs or an OEM developing scalable, standardized systems, the OMRON Robotics Packaging Library provides the tools to simplify integration and reduce engineering time. Here’s how the Robotics Packaging Library helps you improve performance and reduce complexity in packaging automation.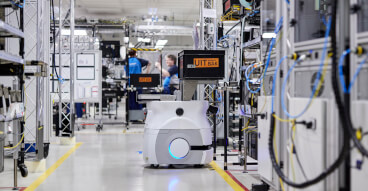
Dynamic lineside replenishment: a strategic response to today’s manufacturing challenges
15 July, 2024 It’s time for a rethink on lineside replenishment systems and practices, if manufacturers are to remain efficient and competitive whilst meeting the challenges posed by customisation and labour shortages. Could AMRs and cobots be the answer? The customisation trend has created numerous operational challenges for manufacturers; the need to accommodate a wider array of components and materials introduces variability that traditional systems struggle to manage efficiently. This can lead to increased inventory costs, longer lead times and production delays. Empirical data underscores the impact of customisation on manufacturing operations; manufacturers reported to have faced extended lead times, higher production costs, and the need to manage multiple inventories. These figures illustrate the tangible challenges that customisation poses, necessitating innovative approaches to manage this complexity efficiently.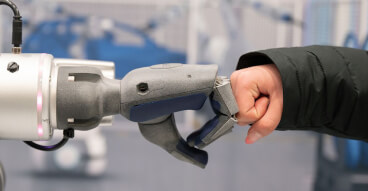
Robotic Trends 2024: Simple and flexible application essential to reach full potential
15 July, 2024 From load carrier to colleague to team player: the role of robots has changed dramatically over the past seven decades. AI is creating more possibilities, but humans remain the determining factor. Robots or humans – who will determine production in the future? Since George Devol's 1954 patent for a programmable manipulator, this question has sparked debate. Devol's Unimate robot revolutionized industry by safely performing dangerous tasks, highlighting that the focus isn't robots vs. humans but rather "robot + human = efficiency." Over 70 years, industry demands have evolved to prioritize flexibility, scalability, adaptability, and sustainability. Robots handle tasks that free humans to focus on value-added activities.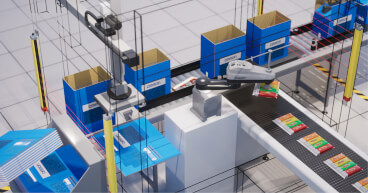
Joining the dots: Automating feeding activities for a competitive advantage
18 June, 2024 Developments in robotics are facilitating the conception of flexible line-side feeding and handling systems that can enhance safety, productivity and quality whilst addressing labour shortages. Factory automation usually starts with the dots. By this we mean the big ticket plant that performs complex and visibly value-adding tasks - whether that is flow wrapping, injection moulding, blister packing, bottling, palletising or other core manufacturing processes. The lines that join those dots together - handling, loading and feeding systems - tend to be more of an afterthought, to the point where these activities are often carried out manually. It might seem easier and cheaper to have an operator loading raw materials onto the production line, or feeding components into machines, rather than spending on automation. But this is a shortsighted view that misses the many business benefits that automated line-side feeding and handling can deliver in terms of efficiency, product quality, scalability and health & safety. It is also a view that is increasingly outdated given the pressure that the current labour crisis is exerting on the manufacturing sector.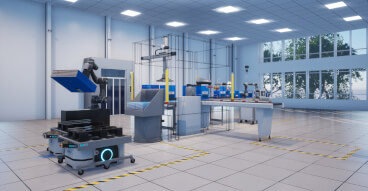
Embracing change: Breaking down the process of flexible manufacturing
30 January, 2024 The fast-moving consumer goods market is experiencing a transformative shift, driven by factors such as consumer empowerment, customization demands, health-conscious preferences, veganism, ethical concerns, and sustainability. We expect that it will undergo more changes in the next decade than it has in the previous 50 years. This necessitates the adaptation of production and supply chains to meet emerging trends. The future of fast-moving consumer goods factories will likely involve smaller, smarter facilities with autonomous movement of goods and interconnected systems.Machines, whether standalone or interconnected, need to be more flexible than ever before to ensure the timely supply of appropriate materials and packaging. Production has to be more agile, increasingly producing retail-ready items with a high mix-low volume approach with zero recalls. The question is how to realize this with minimal cost and fast ROI?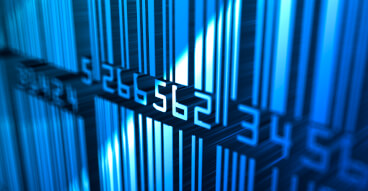
Revolutionise Automotive Manufacturing: Navigating the Traceability Frontier
08 January, 2024 The automotive industry is undergoing transformative shifts, marked by a transition to globalised platforms and standardised vehicle architectures. While this evolution enhances production efficiency, it simultaneously amplifies the impact of a single flawed part, raising the stakes for manufacturers. With the soaring costs of recalls and the intricacies of an ever-changing regulatory landscape, automotive production finds itself at the crossroads of complexity.Traceability emerges as a pivotal solution, promising to mitigate risks and enhance overall operational resilience. However, the prospect of marking up to 20,000 parts per vehicle triggers a valid concern among manufacturers. Is the effort truly worth the potential benefits? The challenge extends beyond mere marking to the implementation of reading and verification technology, coupled with the integration of sophisticated software solutions capable of harnessing the wealth of generated data. Download the whitepaper now to unlock a roadmap for success in navigating the intricate landscape of automotive traceability. Stay ahead of the curve and transform challenges into opportunities with the knowledge shared in this indispensable resource. Our whitepaper delves deep into the current trends and challenges of automotive traceability, unravelling the complexities that manufacturers face. Discover insightful strategies that not only justify the effort but also elevate the effectiveness of a real-time traceability system.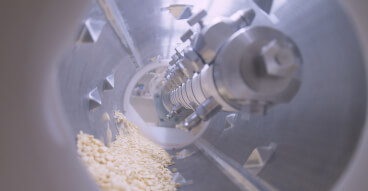
Unlock the Potential of UDI Compliance: Navigate the UDI Mandate with Confidence
08 January, 2024 Complying with the unique device identifier (UDI) system requirements is a critical milestone for medical device manufacturers, distributors, and end users. Ensuring compliance is not just about meeting a regulatory deadline; it's about safeguarding the integrity and safety of medical devices throughout their lifecycle in Europe and the United States.Our comprehensive whitepaper, "Ready for the UDI Mandate Deadline?" dives into the intricacies of UDI implementation, shedding light on the complexities beyond the surface. The ultimate goal is clear – to effectively identify and trace medical devices, from a simple bedpan to a lifesaving artificial heart, promoting safety across the healthcare landscape.However, the journey towards UDI compliance goes beyond merely affixing a printed barcode to a package. Establishing a robust system for verifying UDI markings, and ideally automating these processes, requires a thorough understanding of the means and methods involved. Inline verification during label generation and off-line validation in active service are pivotal components of a successful UDI system.In this whitepaper, we not only outline the UDI labeling requirements but also provide actionable insights into best practices. Discover how the medical device industry can ensure that marking methods are not only compliant but also meticulously verifiable. Elevate your understanding of UDI implementation and gain confidence in navigating the intricacies of the mandate.Don't miss out on this opportunity to empower your organisation with the knowledge needed to thrive in the era of UDI compliance. Download our whitepaper now to stay ahead in the evolving landscape of medical device regulations.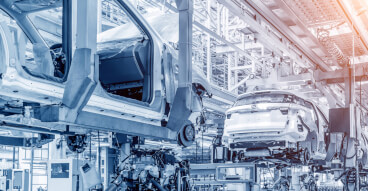
Discover the Power of Flexibility: Navigating Complexity in the Automotive Industry
08 January, 2024 In the dynamic landscape of the automotive industry, adaptation is the key to success. Just as engineers refine vehicles for optimal performance, manufacturers must streamline their operations to navigate the challenges of an ever-evolving market. Embracing flexibility has become a strategic imperative for automakers striving to customise products, boost output, and meet the specific demands of diverse market segments.Uncover the secrets to enhancing throughput and slashing time-to-market while swiftly responding to shifts in demand. While there are costs associated with flexibility – from equipment investments to a slight reduction in throughput during product changeovers – these pale in comparison to the potential expenses incurred by producing unsold vehicles or maintaining idle production lines.Our whitepaper delves into the latest flexible manufacturing trends shaping the automotive industry. Explore effective strategies for overcoming common challenges associated with implementing flexibility, including: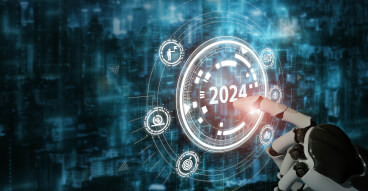
What’s in store for automation in 2024? Six predictions from OMRON Europe
13 December, 2023 The succession of shocks over the last few years has heralded a new era of heightened geopolitical and economic risk. This is prompting manufacturers to build resilience and flexibility into business models and rethink global supply chains and relationships. At the same time, pressure is mounting to incorporate ESG principles into operational decision making. AI, data science, digital twins and sensing, monitoring and vision technology will all be essential to developing automation and control solutions that can help the manufacturing industry adapt to this new reality. In this context, I would like to share the top six trends that will impact and shape industrial automation in 2024 and beyond.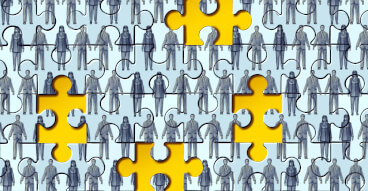
Top 4 Ways to Tackle Labour Shortage with Automation
06 September, 2023 Automation is a pathway to supporting manual workforce and not replacing them.Labour shortages in manufacturing are a growing cause of concern worldwide. While financial incentives and targeted workforce qualifications have been used as countermeasures, more innovative solutions are needed. Many manufacturers choose to automate repetitive activities but to what extent is it supporting the existing taskforce or is it taking away their jobs altogether?In 2023, Reuters disclosed an alarming trend: a record-high 53% of companies grapple with hiring difficulties. Staff shortages, soaring energy costs, combined with the pursuit of climate neutrality create new challenges. In the quest for sustainable manufacturing, innovative strategies to address labour gaps and enhance existing talent are the beacon of progress.Let us go over the top four ways to addressing the labour shortage and supporting the current workforce with automation: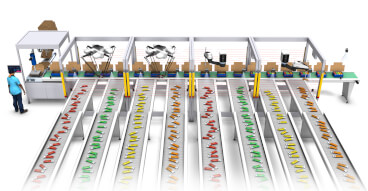
Easy programming
21 June, 2023 Omron Automation robotics are designed to be easy to program, even for users who have little or no experience with robotics. The robots can be programmed using intuitive software, and they can be taught new tasks through a simple "teach and playback" process. This makes it easy for manufacturers to integrate robotics into their production processes and improve their Pick & Place operations. With easy programming, manufacturers can reduce the learning curve and training time for operators, allowing them to get up and running quickly.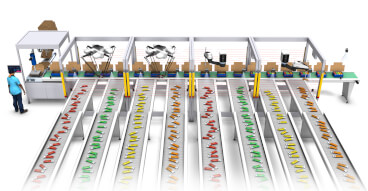
High-speed and precision movements
14 June, 2023 Omron Automation robotics are designed for high-speed and precision movements, which make them ideal for Pick & Place applications. The robots can pick up and place objects quickly and accurately, reducing cycle times and increasing productivity. Omron robots can move at high speeds without sacrificing precision, which is essential for Pick & Place applications where objects need to be placed in precise locations. With Omron Automation robotics, manufacturers can improve their production efficiency.Pick & Place applications are a common task in industrial settings, where objects need to be moved from one place to another quickly and accurately. This can be a repetitive and time-consuming task that can be automated using robotics solutions. In this blog post, we will explore how robotics can help with Pick & Place applications and improve productivity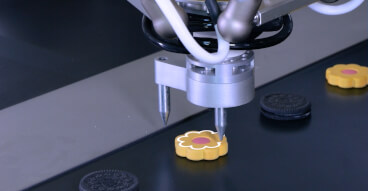
Creating smarter, faster, and simpler multi-robot packaging lines?
16 January, 2025 Does integrating robotics into a packaging line feel like solving a puzzle with too many pieces? Designing a high-performing packaging line with multiple robots often involves navigating complex integrations, precise motion control, and the need to meet tight production demands. Whether you are a System Integrator crafting tailored solutions for specific client needs or an OEM developing scalable, standardized systems, the OMRON Robotics Packaging Library provides the tools to simplify integration and reduce engineering time. Here’s how the Robotics Packaging Library helps you improve performance and reduce complexity in packaging automation.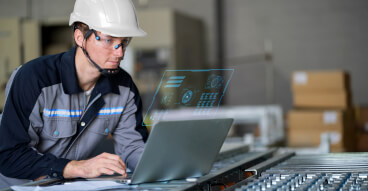
Navigating the new machinery directive
16 January, 2025 The European Union’s transition from the 2006/42/EC Machinery Directive to the new Machinery Regulation (2023/1230/EU), effective January 20, 2027, represents a significant shift in legislative requirements for machinery and related products. For system integrators, the regulation introduces stricter requirements for the incorporation of AI-driven systems, autonomous machines, and interconnected equipment. For end users, especially those operating complex machinery systems, preparing for these changes is a strategic necessity.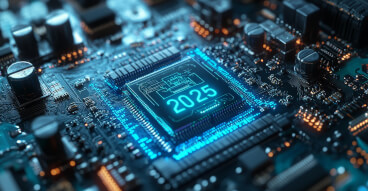
From optimization to autonomy - Top five manufacturing automation trends for 2025 from OMRON
04 January, 2025 As we step into 2025, the world of industrial automation is approaching a new chapter. According to OMRON's SINIC Theory, which ties technological advances to societal change, we’re now moving from the Optimization Society to the Autonomous Society. The theory, created in 1970 by OMRON’s founder Kazuma Tateishi, predicts future societal and technological developments to guide innovation. In the Optimization phase, the focus has been on refining processes, boosting efficiency, and using technology to improve operations. But the Autonomous Society is a whole new era—one where systems don’t just run efficiently; they become self-regulating, self-learning, and capable of independent decision-making.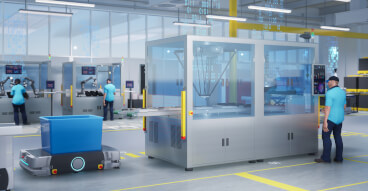
Securing a battery-powered future through automated recycling
17 December, 2024 Batteries have a crucial role to play in facilitating the scaling up of renewables in the power mix and the electrification of transport, as we transition away from fossil fuel dependence and towards cleaner energy technologies to meet the targets agreed at COP 28.This has sent the battery market on an upwards trajectory, with two sectors - power and transport - driving demand. According to the International Energy Agency (IEA), the energy sector accounts for over 90% of overall battery demand. It reported that in 2023 alone, battery deployment in this sector increased by more than 130% year-on-year, adding a total of 42 gigawatts (GW) to electricity systems around the world. Energy storage is emerging as a major application for batteries as a means of capturing renewable energy and is only going to become more important in the future. In the transport sector, meanwhile, batteries have facilitated the rise of electric cars, bikes, trucks, buses and other battery-powered vehicles.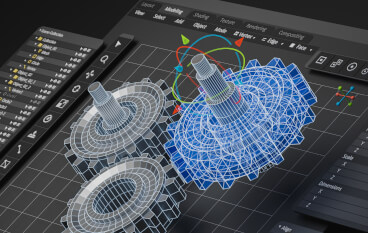
Taking the first steps to successful digitalisation
12 November, 2024 Building a digital factory isn’t an end or a reason in itself. A digital factory is a tool that gives manufacturing businesses the flexibility to respond to changes in the market - whether that is innovation trends or cost increases, and whether they are operating in the food & beverage, personal care, pharmaceutical or automotive sector.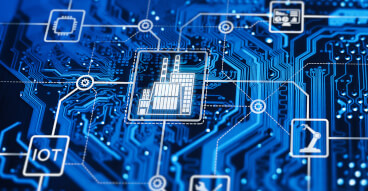
Digitising with open standards: the recipe for a good night’s sleep
02 September, 2024 Can we commit to the predictions I have made? Will we be able to deliver to the deadline? Do I have enough insight to know for sure? How is the factory doing in terms of QCDE (quality, cost, delivery time and environmental impact) against our targets and compared to the competition? These are some of the concerns that keep factory managers awake at night; concerns that can be addressed through digitisation. In a digitised production environment, factory managers don’t have to worry about the unknowns, the risks and the might-happens. Digitisation eliminates uncertainty and enables performance-driven optimisation. It provides insights that can help factory managers improve quality, reduce cost, shorten lead times and reduce environmental impact. The manager of a digitised factory shouldn’t wake up worrying in the middle of the night, but if they do, a brief glance at their mobile phone should reassure them that everything is running as it should be. However, moving from a state of anxiety-induced insomnia to one of blissful somnolence is not easy. Put bluntly, digitisation can be quite tedious. Project leaders rarely have the luxury of working with a blank canvas; most of the time they are working with a patchwork quilt of old technologies sewn together; they are trying to digitise production lines incorporating machines that have never logged data and were built before data communication protocols even existed. This all adds up to a sizeable OT and IT integration challenge.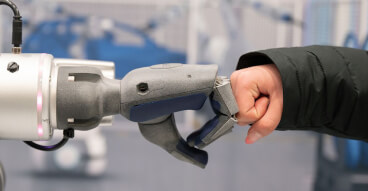
Robotic Trends 2024: Simple and flexible application essential to reach full potential
15 July, 2024 From load carrier to colleague to team player: the role of robots has changed dramatically over the past seven decades. AI is creating more possibilities, but humans remain the determining factor. Robots or humans – who will determine production in the future? Since George Devol's 1954 patent for a programmable manipulator, this question has sparked debate. Devol's Unimate robot revolutionized industry by safely performing dangerous tasks, highlighting that the focus isn't robots vs. humans but rather "robot + human = efficiency." Over 70 years, industry demands have evolved to prioritize flexibility, scalability, adaptability, and sustainability. Robots handle tasks that free humans to focus on value-added activities.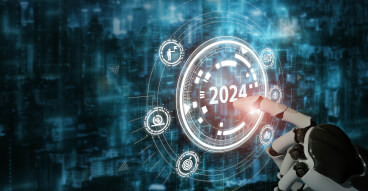
What’s in store for automation in 2024? Six predictions from OMRON Europe
13 December, 2023 The succession of shocks over the last few years has heralded a new era of heightened geopolitical and economic risk. This is prompting manufacturers to build resilience and flexibility into business models and rethink global supply chains and relationships. At the same time, pressure is mounting to incorporate ESG principles into operational decision making. AI, data science, digital twins and sensing, monitoring and vision technology will all be essential to developing automation and control solutions that can help the manufacturing industry adapt to this new reality. In this context, I would like to share the top six trends that will impact and shape industrial automation in 2024 and beyond.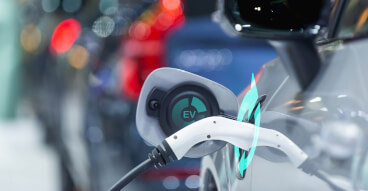
EV transition made easy: Top three challenges to overcome in automotive manufacturing
23 November, 2023 The transition to electric vehicles is a challenging path for automotive manufacturers. Long-established companies that have traditionally produced vehicles with combustion engines are now venturing into an entirely new realm of vehicle platforms. Let us investigate the top challenges facing the electric vehicle manufacturing industry and explore the latest innovative solutions on the horizon.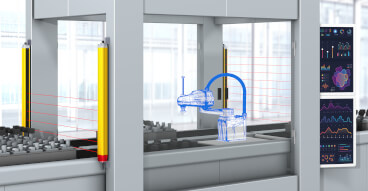
A meeting of minds: IT/OT convergence in industrial automation
22 September, 2023 Future-focused manufacturers are edging closer to their ideals of flexible, efficient and sustainable production by exploring digital transformation in earnest. However, as interest in digitalisation builds, it is becoming apparent that a huge gulf exists between the worlds of OT (Operational Technology) and IT (Information Technology). And this divide needs to be bridged if today’s visions for factories of the future are to become tomorrow’s reality.But before we look at why a convergence of IT and OT is necessary and how this can be achieved, let’s take a step back to basics and clear up some misunderstandings around the terminology.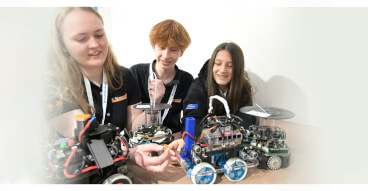
Empowering the workforce: OMRON's approach to skills development in European manufacturing
06 September, 2023 Delving into OMRON's unwavering commitment to nurturing skills that empower the next generation, while the industry embarks on a transformative journey – a journey that unlocks the full potential of the Fourth Industrial Revolution (4IR) while boldly moving towards the Fifth Industrial Revolution (5IR).In the halls of academia, the boardrooms of visionary business leaders, and the chambers of forward-thinking politicians, a fervent debate evokes. It revolves around the profound shift from the Fourth Industrial Revolution, 4IR, or Industry 4.0 as it is also known, to Industry 5.0 will change the world in which we live.Historically the Industrial Revolution was the First Machine Age, and electricity the Second, then electronics was the Third, and the internet as platform the Fourth Machine Age. We are now entering the Fifth Machine Age, which highlights harmonious human-machine collaboration and the contributions of the industry to society. This is the moment to not only adapt but to lead, to pioneer, and to create a future where innovation knows no bounds. Klaus Schwab, the founder and executive chairman of the World Economic Forum has observed that: “We stand on the brink of a technological revolution that will fundamentally alter the way we live, work, and relate to one another. In its scale, scope, and complexity, the transformation will be unlike anything humankind has experienced before. Our world is undergoing a transformative shift. Global production is evolving, driven by the automation of traditional industrial practices through smart technology, M2M communication, and IoT integration. This synergy fuels heightened automation, seamless communication, and intelligent machines that autonomously analyse and diagnose challenges.The rise of AI sparks debates, hinting at deeper transformations within our societal tapestry. As we navigate this dynamic landscape, we are poised to embrace innovation and reshape our future.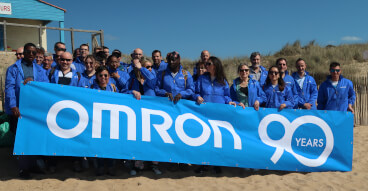
From red lights to robots: OMRON celebrates 90 years of innovation
06 June, 2023 This year on Founder’s Day, OMRON looked back on 90 years of pushing technological boundaries, and looks forward to a future of automation innovation framed by sustainability, digitalisation and human-machine collaboration.May the 10th be with you… Every year, 10th May is probably the most important day in OMRON’s calendar. On this day, 30,000 OMRON employees around the world celebrate the life and legacy of the company’s founder, Kazuma Tateishi. They do this by recommitting to Tateishi’s vision of using technology to create a better world and by giving back to society - often by participating in volunteer and charity projects in their communities. Innovation Milestones OMRON's journey of innovation began in 1933 with the development of a high-precision timer for X-ray photography. This marked the company's first contribution to addressing societal needs. In 1960, OMRON unveiled the world's first non-contact proximity switch, revolutionizing advanced mass production capabilities. Since then, OMRON has continued to introduce groundbreaking technologies, including the first automatic traffic signal, unmanned train station system, wearable blood pressure controller, ultra-high-speed fuzzy logical controller, and automatic cancer cell diagnostic equipment.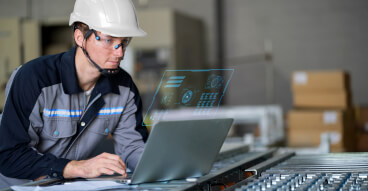
Navigating the new machinery directive
16 January, 2025 The European Union’s transition from the 2006/42/EC Machinery Directive to the new Machinery Regulation (2023/1230/EU), effective January 20, 2027, represents a significant shift in legislative requirements for machinery and related products. For system integrators, the regulation introduces stricter requirements for the incorporation of AI-driven systems, autonomous machines, and interconnected equipment. For end users, especially those operating complex machinery systems, preparing for these changes is a strategic necessity.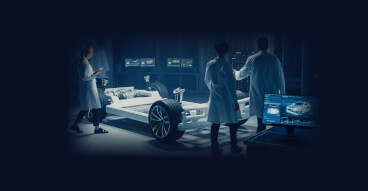
Why automated inspection systems are critical for electric vehicle manufacturing
23 March, 2023 Safety trumps all other concerns in the automotive industry, and electric vehicle manufacturing is no exception. However, safety can also introduce complexity, and the complexity of today’s vehicles – particularly EVs – is such that manufacturers are no longer able to rely on traditional sample or audit-based inspection methods.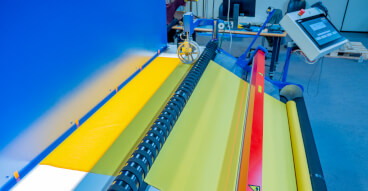
Vadain automates the inspection of curtain fabrics with machine vision
08 April, 2022 Vadain, the market leader in custom curtains in the Netherlands, needed a solution to detect errors as early as possible in kilometers of curtain fabrics. Together with software developers from Sycade, OMRON machine vision technology, and machine builder Eisenkolb, they developed an automated solution to detect and analyze errors in curtain fabrics, making the time-consuming manual inspection process a thing of the past.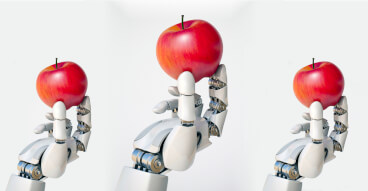
Factory automation: four tips for the future of food & beverage manufacturing
16 July, 2020 The coronavirus pandemic has posed major challenges to organisations of all types and sizes. In the food and commodity industry, companies have faced significantly reduced consumption and disrupted supply chains, while at-home consumption increased, and out-of-home consumption came near to a standstill. But how can manufacturers adapt their business strategies and production processes both now and in the longer term? The pandemic may provide an opportunity for rethinking outdated processes and procedures and enhancing them with concepts such as innovative robotics, sensor technology and holistic automation strategies.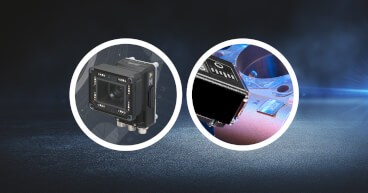
Six challenges for brand protection
19 November, 2019 Brand protection is an important topic for any business. But as industrial companies invest in new technology, such as smart robotics, artificial intelligence and vision systems, are they aware of the key challenges that could affect their brand?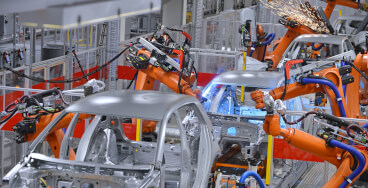
Legacy of machine vision
16 October, 2019 Did you know that for more than 40 years, Omron has developed vision sensing technologies for factory automation, surveillance and transport systems, and more recently for facial recognition and image processing for mobile phones, and even driver monitoring for autonomous driving?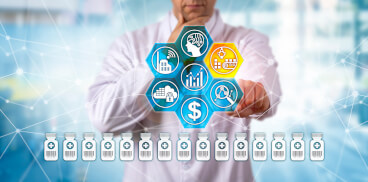
Late-stage customization in pharmaceutical manufacturing
16 October, 2019 As a result of serialization legislation, pharmaceutical manufacturers must now ensure that labels printed at a late stage contain all of the data required for compliance. This includes customizing product labels for certain markets, customers or products by adding variable data to labels or packaging. This avoids the need to stock individual packaging materials for each variant.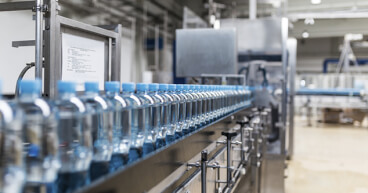
How to secure FMCG supply chains with traceability?
02 October, 2019 The traceability of food and drink products throughout the production and distribution process can be a complex issue. For example, alcoholic drink producers need systems that enable them to comply with local regulations regarding food traceability, as well as tax legislation.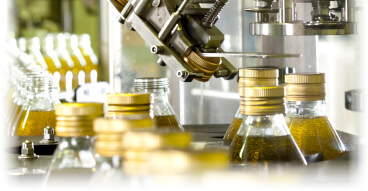
Barcodes: keeping track of product quality
02 October, 2019 For many years, barcode technology has proved to be an economical and flexible identification technology. It has continued to develop and as a result, 1D and 2D codes (such as Datamatrix) are now used almost universally. Their versatility have made them a popular choice for streamlining many key supply chain processes, including production, logistics and item traceability.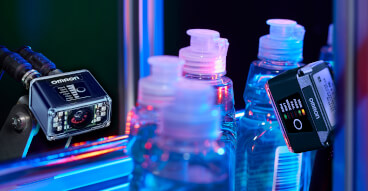
Revolutionising Quality Control: AI and Data Capture Transform Manufacturing
12 March, 2025 Maintaining consistent product quality in modern manufacturing can feel like a relentless challenge. Just as one issue is resolved, another arises to test your processes to their limits. Whether you're a production manager keeping the assembly line efficient, an engineer integrating new technologies, a salesperson offering innovative solutions, or a machine builder designing the next generation of equipment, product defects are a common hurdle.But what if there was a way to significantly reduce these defects, meet regulatory requirements with ease, and enhance overall business performance? Next generation technologies leveraging Artificial Intelligence (AI) and advanced product data capture may be the solutions you need.Specifically, we are referring to four cutting-edge technologies making a significant impact on quality control: Automated Traceability: Monitoring every product's journey through data capture. AI Vision Systems: Enhancing inspection beyond human capabilities. Digital Watermarking: Protecting product integrity through embedded data. AI-Driven Sealing Solutions: Perfecting packaging with intelligent adjustments. In this blog, we’ll explore how these technologies can help you achieve excellence in quality control, no matter your role in the manufacturing sector.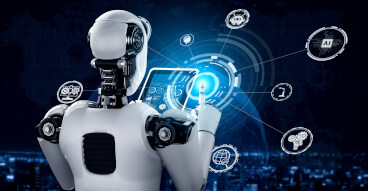
Optimising Production: How Smart Maintenance Technologies Are Changing the Game
21 January, 2025 Unplanned downtime is sabotaging production goals. It's time to take action.Unexpected machine stoppages aren't just inconveniences—they represent costly disruptions that derail schedules, increase operational expenses, and reduce profitability. Efficiency and reliability are crucial factors for maintaining competitiveness in manufacturing, so, minimising productivity losses such as unplanned downtime must be a strategic priority for both small and medium enterprises (SMEs) and large corporations.But what if you could anticipate equipment failures before they happen, deploy machines designed with maintenance in mind, and minimise fault finding? Smart maintenance technologies are making all of these a reality, transforming operations from reactive firefighting to proactive problem-solving.In this blog, we’ll explore how predictive maintenance, intelligent machine design, and advanced diagnostics are helping manufacturers reduce downtime, optimise costs, and stay ahead in an ever-evolving industry.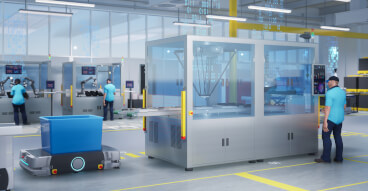
Securing a battery-powered future through automated recycling
17 December, 2024 Batteries have a crucial role to play in facilitating the scaling up of renewables in the power mix and the electrification of transport, as we transition away from fossil fuel dependence and towards cleaner energy technologies to meet the targets agreed at COP 28.This has sent the battery market on an upwards trajectory, with two sectors - power and transport - driving demand. According to the International Energy Agency (IEA), the energy sector accounts for over 90% of overall battery demand. It reported that in 2023 alone, battery deployment in this sector increased by more than 130% year-on-year, adding a total of 42 gigawatts (GW) to electricity systems around the world. Energy storage is emerging as a major application for batteries as a means of capturing renewable energy and is only going to become more important in the future. In the transport sector, meanwhile, batteries have facilitated the rise of electric cars, bikes, trucks, buses and other battery-powered vehicles.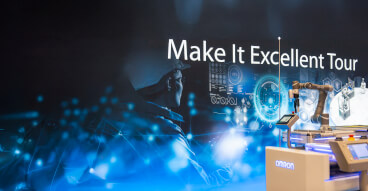
Beyond tech for tech’s sake: What happens when industrial automation meets operational excellence
30 November, 2024 The past few years have seen rapid technological advancements, with the rise of AI standing out as a key trend. In a survey of manufacturers across the UK, US, and Canada, 70% said they had implemented some form of AI into their operations. This willingness to embrace new technologies is impressive, especially since manufacturing industries have so much to gain from automation.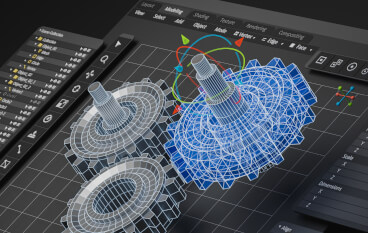
Taking the first steps to successful digitalisation
12 November, 2024 Building a digital factory isn’t an end or a reason in itself. A digital factory is a tool that gives manufacturing businesses the flexibility to respond to changes in the market - whether that is innovation trends or cost increases, and whether they are operating in the food & beverage, personal care, pharmaceutical or automotive sector.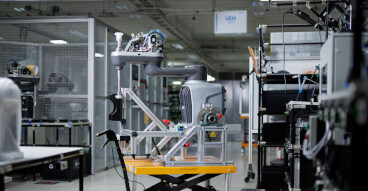
Avoiding efficiency blockage: Why companies should not postpone their robotics plans?
24 September, 2024 Delaying investments in innovative technologies is associated with numerous risks. Companies that are still hesitant should ask themselves three questions.The European economy faces a range of challenges that impact its growth, stability, and competitiveness. Europe, for example, has one of the oldest populations in the world. An aging workforce increases the burden on social security systems and reduces the labor supply, potentially slowing economic growth. Furthermore, the EU's commitment to the Green Deal and achieving carbon neutrality by 2050 requires substantial investments and structural changes in various sectors. Added to this is a lack of willingness to invest due to financial worries. A recent study by the McKinsey Global Institute (MGI) found that large European firms with more than $1 billion in revenue have fallen behind their US counterparts. They collectively invest $400 billion a year less and grow one-third more slowly.This investment fatigue can lead to several problems that have both short- and long-term effects, including disadvantages in terms of competitiveness, sustainability, and reputation, lower productivity, and less success in attracting new skilled workers. Innovative robotics can counteract such developments but also requires well-thought-out financing. Therefore, companies that are currently limiting their investments should urgently ask themselves whether this will not have more negative consequences for them in the long term than short-term savings. The following three questions should be the focus of such considerations: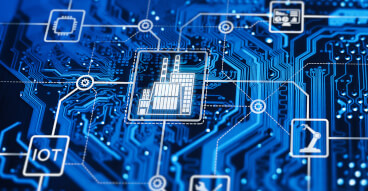
Digitising with open standards: the recipe for a good night’s sleep
02 September, 2024 Can we commit to the predictions I have made? Will we be able to deliver to the deadline? Do I have enough insight to know for sure? How is the factory doing in terms of QCDE (quality, cost, delivery time and environmental impact) against our targets and compared to the competition? These are some of the concerns that keep factory managers awake at night; concerns that can be addressed through digitisation. In a digitised production environment, factory managers don’t have to worry about the unknowns, the risks and the might-happens. Digitisation eliminates uncertainty and enables performance-driven optimisation. It provides insights that can help factory managers improve quality, reduce cost, shorten lead times and reduce environmental impact. The manager of a digitised factory shouldn’t wake up worrying in the middle of the night, but if they do, a brief glance at their mobile phone should reassure them that everything is running as it should be. However, moving from a state of anxiety-induced insomnia to one of blissful somnolence is not easy. Put bluntly, digitisation can be quite tedious. Project leaders rarely have the luxury of working with a blank canvas; most of the time they are working with a patchwork quilt of old technologies sewn together; they are trying to digitise production lines incorporating machines that have never logged data and were built before data communication protocols even existed. This all adds up to a sizeable OT and IT integration challenge.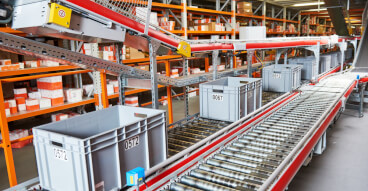
Transforming Logistics with Automation: Meeting Diverse Client Demands
05 June, 2024 The logistics landscape is evolving, with clients increasingly expecting comprehensive services, including personalised, customised, and seasonal packaging alongside various value-added services.Personalised Packaging:Consumers now want products that meet their exact specifications. This trend spans from everyday items to luxury goods, making it challenging to ensure the correct product is paired with the appropriate personalised packaging. The personalised packaging market is growing at over 5% annually. Surveys indicate that over half of consumers are more likely to repurchase from a vendor if they receive a product in personalised packaging.Customised Packaging:Customised packaging caters to specific client branding requirements to appeal to particular market segments, such as bulk-to-brand packaging in the retail sector for products like instant coffee, baby formula, or sealed foods. This often necessitates batch runs, which can be inefficient for manufacturers. Market research by Nielsen shows that 55% of consumers are willing to pay more for products designed for their segment or demographic group.Seasonal Packaging:Seasonal packaging significantly influences consumer buying decisions. A survey by the Paper and Packaging Board found that 44% of consumers say festive packaging increases their excitement about a product. Additionally, 60% of consumers are likely to share pictures of seasonally packaged products on social media, enhancing brand visibility and engagement.Many clients now request value-added services, including co-packing, labelling, and other enhancements that prepare the product for the consumer market.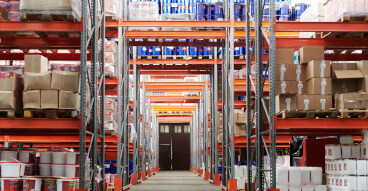
The Future of Storing and Moving Stuff: Why Trying New Things and Teamwork Matter
10 April, 2024 In the rapidly evolving world of logistics, the industry dedicated to storing and moving goods is at a pivotal moment, marked by both unprecedented growth and daunting challenges. Over the last decade, storage space, particularly in the form of warehouses, has seen a remarkable expansion. Specifically, shed space has grown by 61% in the last decade and an impressive 22% in just the last three years. Despite the recent slowdown in e-commerce activity caused by the increased cost of living, the trend since 2015 is overwhelmingly positive and will continue to drive a strong demand for warehouse space in the future. However, as these storage spaces become more common, the industry faces a significant challenge: a growing labour shortage that threatens to slow down its expansion.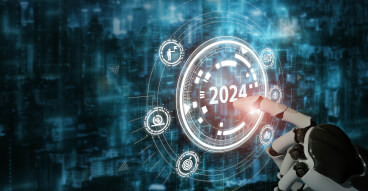
What’s in store for automation in 2024? Six predictions from OMRON Europe
13 December, 2023 The succession of shocks over the last few years has heralded a new era of heightened geopolitical and economic risk. This is prompting manufacturers to build resilience and flexibility into business models and rethink global supply chains and relationships. At the same time, pressure is mounting to incorporate ESG principles into operational decision making. AI, data science, digital twins and sensing, monitoring and vision technology will all be essential to developing automation and control solutions that can help the manufacturing industry adapt to this new reality. In this context, I would like to share the top six trends that will impact and shape industrial automation in 2024 and beyond.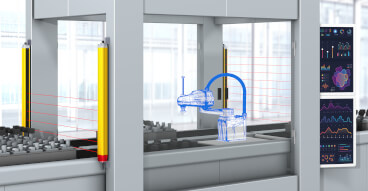
A meeting of minds: IT/OT convergence in industrial automation
22 September, 2023 Future-focused manufacturers are edging closer to their ideals of flexible, efficient and sustainable production by exploring digital transformation in earnest. However, as interest in digitalisation builds, it is becoming apparent that a huge gulf exists between the worlds of OT (Operational Technology) and IT (Information Technology). And this divide needs to be bridged if today’s visions for factories of the future are to become tomorrow’s reality.But before we look at why a convergence of IT and OT is necessary and how this can be achieved, let’s take a step back to basics and clear up some misunderstandings around the terminology.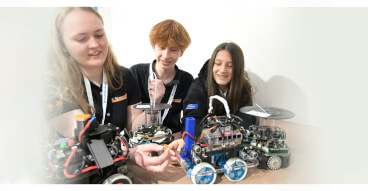
Empowering the workforce: OMRON's approach to skills development in European manufacturing
06 September, 2023 Delving into OMRON's unwavering commitment to nurturing skills that empower the next generation, while the industry embarks on a transformative journey – a journey that unlocks the full potential of the Fourth Industrial Revolution (4IR) while boldly moving towards the Fifth Industrial Revolution (5IR).In the halls of academia, the boardrooms of visionary business leaders, and the chambers of forward-thinking politicians, a fervent debate evokes. It revolves around the profound shift from the Fourth Industrial Revolution, 4IR, or Industry 4.0 as it is also known, to Industry 5.0 will change the world in which we live.Historically the Industrial Revolution was the First Machine Age, and electricity the Second, then electronics was the Third, and the internet as platform the Fourth Machine Age. We are now entering the Fifth Machine Age, which highlights harmonious human-machine collaboration and the contributions of the industry to society. This is the moment to not only adapt but to lead, to pioneer, and to create a future where innovation knows no bounds. Klaus Schwab, the founder and executive chairman of the World Economic Forum has observed that: “We stand on the brink of a technological revolution that will fundamentally alter the way we live, work, and relate to one another. In its scale, scope, and complexity, the transformation will be unlike anything humankind has experienced before. Our world is undergoing a transformative shift. Global production is evolving, driven by the automation of traditional industrial practices through smart technology, M2M communication, and IoT integration. This synergy fuels heightened automation, seamless communication, and intelligent machines that autonomously analyse and diagnose challenges.The rise of AI sparks debates, hinting at deeper transformations within our societal tapestry. As we navigate this dynamic landscape, we are poised to embrace innovation and reshape our future.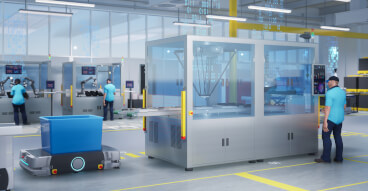
Securing a battery-powered future through automated recycling
17 December, 2024 Batteries have a crucial role to play in facilitating the scaling up of renewables in the power mix and the electrification of transport, as we transition away from fossil fuel dependence and towards cleaner energy technologies to meet the targets agreed at COP 28.This has sent the battery market on an upwards trajectory, with two sectors - power and transport - driving demand. According to the International Energy Agency (IEA), the energy sector accounts for over 90% of overall battery demand. It reported that in 2023 alone, battery deployment in this sector increased by more than 130% year-on-year, adding a total of 42 gigawatts (GW) to electricity systems around the world. Energy storage is emerging as a major application for batteries as a means of capturing renewable energy and is only going to become more important in the future. In the transport sector, meanwhile, batteries have facilitated the rise of electric cars, bikes, trucks, buses and other battery-powered vehicles.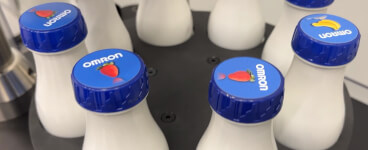
PPWR: why cross-chain collaboration, traceability and smart packaging are key
24 September, 2024 According to Eurostat figures, in 2021, each person living in the EU generated 188.7 kg packaging - almost 32 kg more than in 2011. Over this period, the amount of plastic packaging waste increased by 27%. Whilst recycling rates have also increased, a large volume of plastic packaging is still not being recycled - the latest statistics suggest that only a handful of countries in Europe are achieving a 50% recycling rate for plastics. Recognising that the existing legal framework was failing to drive improvement in packaging waste reduction, in 2022 the Commission proposed a revision to the 2018 directive for Packaging and Packaging Waste Regulation (PPWR).The revised PPWR is expected to enter into force by end of this year, and will fundamentally change the way packaging is designed, consumed and disposed of. The updated regulation is broad in its scope, but the underlying aims are to reduce the amount of packaging waste generated and increase packaging recyclability.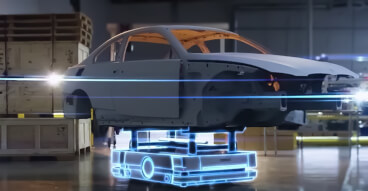
Top 4 challenges EV manufacturers face in their journey to achieving a sustainable future
17 June, 2024 Electric vehicles (EVs) have transitioned from a niche market to a major industry force in recent years. As of 2023, electric cars account for nearly one in five vehicles sold, with sales increasing by 3.5 million units—a 35% jump from the previous year, according to the IEA's Global EV Outlook 2024. This surge is expected to continue, with projections indicating that sales in emerging markets will exceed 1 million units in 2024, marking a 40% increase from 2023. Governments worldwide are pushing to reduce CO2 emissions, which is speeding up this shift to electric vehicles.So, what does this mean for automotive manufacturers? First, it means they need to pivot to designing and producing predominantly electric fleets, a move many have already started. Second, it means building new production lines and mastering new manufacturing processes, which can be quite a challenge.This is where a trusted automation partner comes in. Partnering with an expert in automation can help manage the complexities of this industry-wide transition. With a broad technology portfolio, global support, and deep automotive expertise, OMRON is ready to guide manufacturers on their electrified journey.This blog post will explore the top challenges in the EV manufacturing sector and how partnering with OMRON can provide effective solutions: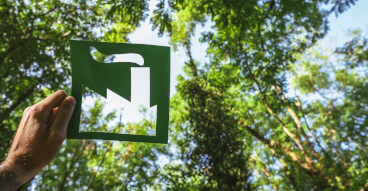
Intelligent automation as an agent of change
31 May, 2024 The manufacturing industry is responsible for around a quarter of global GHG emissions¹, which puts it on a par with transport as the second biggest contributor to carbon emissions. This means that reducing the manufacturing sector’s carbon footprint will play a vital role in mitigating our impact on climate change.It’s time for the manufacturing industry to stop being a source of problems and start living up to its potential by being one of the sources of solutions, addressing climate change and utilising automation as the agent of change in the process.This reflects our founder’s belief that, as a business, we have a responsibility to give back to the society in which we operate. Over 90 years ago, OMRON was born out of the vision of its founder, Kazuma Tateishi, of using technology to create a better world.Tateishi’s ethos of “improving lives and contributing to a better society” has never been more relevant than in the present day, given the climate challenges we face as a society. But how can manufacturing make a positive difference?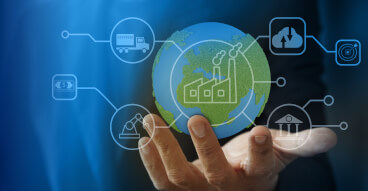
Even if it ain’t broke, you still oughta fix it
04 April, 2024 Making FMCG manufacturing more sustainable through intelligent energy management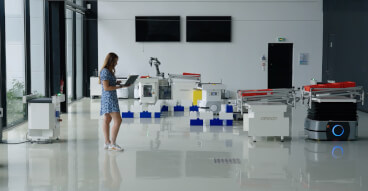
Come on, ladies! Dare to explore exciting career opportunities in automation
01 March, 2024 Maryam Dolatabadi and Asunción Pastrana Costa are experienced automation experts at OMRON. They appeal to girls and women: “Be brave, you are urgently needed in the industry!”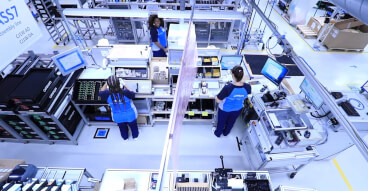
Industrial automation and robotics: still a man’s world?
07 February, 2024 What is it like being a woman in automation today? Three women from OMRON Europe talk about their experiences in the world of industrial automation, the challenges they face, and the tools and support that have helped them to thrive.When Wendy Tonks first started her career in engineering in the UK just over 20 years ago, one of the first ground rules that she had to lay down was that she wasn’t a tea lady.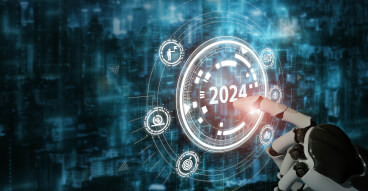
What’s in store for automation in 2024? Six predictions from OMRON Europe
13 December, 2023 The succession of shocks over the last few years has heralded a new era of heightened geopolitical and economic risk. This is prompting manufacturers to build resilience and flexibility into business models and rethink global supply chains and relationships. At the same time, pressure is mounting to incorporate ESG principles into operational decision making. AI, data science, digital twins and sensing, monitoring and vision technology will all be essential to developing automation and control solutions that can help the manufacturing industry adapt to this new reality. In this context, I would like to share the top six trends that will impact and shape industrial automation in 2024 and beyond.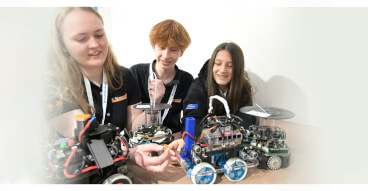
Empowering the workforce: OMRON's approach to skills development in European manufacturing
06 September, 2023 Delving into OMRON's unwavering commitment to nurturing skills that empower the next generation, while the industry embarks on a transformative journey – a journey that unlocks the full potential of the Fourth Industrial Revolution (4IR) while boldly moving towards the Fifth Industrial Revolution (5IR).In the halls of academia, the boardrooms of visionary business leaders, and the chambers of forward-thinking politicians, a fervent debate evokes. It revolves around the profound shift from the Fourth Industrial Revolution, 4IR, or Industry 4.0 as it is also known, to Industry 5.0 will change the world in which we live.Historically the Industrial Revolution was the First Machine Age, and electricity the Second, then electronics was the Third, and the internet as platform the Fourth Machine Age. We are now entering the Fifth Machine Age, which highlights harmonious human-machine collaboration and the contributions of the industry to society. This is the moment to not only adapt but to lead, to pioneer, and to create a future where innovation knows no bounds. Klaus Schwab, the founder and executive chairman of the World Economic Forum has observed that: “We stand on the brink of a technological revolution that will fundamentally alter the way we live, work, and relate to one another. In its scale, scope, and complexity, the transformation will be unlike anything humankind has experienced before. Our world is undergoing a transformative shift. Global production is evolving, driven by the automation of traditional industrial practices through smart technology, M2M communication, and IoT integration. This synergy fuels heightened automation, seamless communication, and intelligent machines that autonomously analyse and diagnose challenges.The rise of AI sparks debates, hinting at deeper transformations within our societal tapestry. As we navigate this dynamic landscape, we are poised to embrace innovation and reshape our future.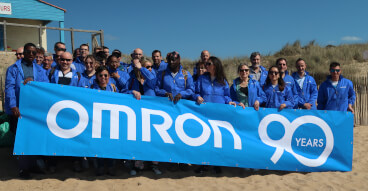
From red lights to robots: OMRON celebrates 90 years of innovation
06 June, 2023 This year on Founder’s Day, OMRON looked back on 90 years of pushing technological boundaries, and looks forward to a future of automation innovation framed by sustainability, digitalisation and human-machine collaboration.May the 10th be with you… Every year, 10th May is probably the most important day in OMRON’s calendar. On this day, 30,000 OMRON employees around the world celebrate the life and legacy of the company’s founder, Kazuma Tateishi. They do this by recommitting to Tateishi’s vision of using technology to create a better world and by giving back to society - often by participating in volunteer and charity projects in their communities. Innovation Milestones OMRON's journey of innovation began in 1933 with the development of a high-precision timer for X-ray photography. This marked the company's first contribution to addressing societal needs. In 1960, OMRON unveiled the world's first non-contact proximity switch, revolutionizing advanced mass production capabilities. Since then, OMRON has continued to introduce groundbreaking technologies, including the first automatic traffic signal, unmanned train station system, wearable blood pressure controller, ultra-high-speed fuzzy logical controller, and automatic cancer cell diagnostic equipment.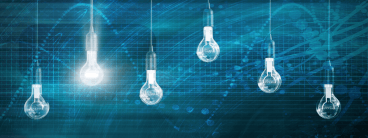
Accelerating socially driven innovation
28 March, 2023 Society is built on cultural norms and values that shape how people think, behave, and interact with each other. These cultural factors can influence everything from consumer preferences and business practices to political beliefs, which in turn affect how manufacturing evolves.Manufacturing is one of the most important sectors of any economy, yet in the UK it can fairly claim to be underrated - despite our being the world’s 9th largest manufacturing nation. According to MAKE UK research, manufacturing provides 2.7 million jobs, has an annual output of £191 billion, and offers wages 13% higher, on average, than the rest of the economy.The sector also has a multiplier effect which extends far beyond the jobs and wealth it creates directly, supporting the growth of other industries and creating a positive cycle of economic growth - boosting the overall productivity of the country and improving lives.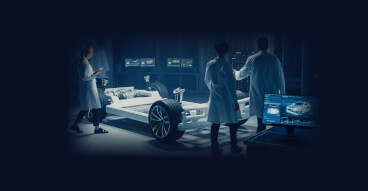