Automation blog

Automation adapts to sustainable packaging
16 August, 2022 Have you ever ordered a small item online, and then felt incensed when it arrived in an oversized box packed out with bubble wrap, air-filled cushions or paper inserts?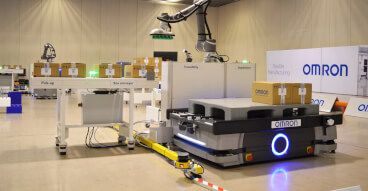
Flexible Manufacturing Roadshow: Taking the factory of the future across Europe
16 June, 2022 What if you could see, feel and touch the factory of the future? What does it take to realize flexible, efficient, and sustainable production? This is the idea behind OMRON’s unique Flexible Manufacturing Roadshow travelling across Europe this year. The roadshow features exclusive demonstrations of human-machine collaborative solutions not usually seen outside of a factory setting due to their size and scale.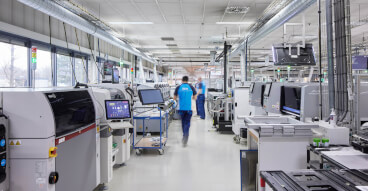
Building the Factory of the Future together
16 June, 2022 As one of the largest business units at OMRON, we aim to further develop the Den Bosch plant to serve the needs in the EMEA region.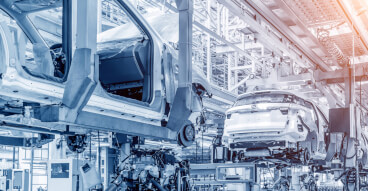
Traceability in Automotive: What decision-makers and experts should look out for now
23 May, 2022 From e-mobility to autonomous driving, from skills shortages to digitalization: The automotive industry is undergoing a profound change, marked, for example, by a shift to globalized platforms and standardized vehicle architectures. On the one hand, production is becoming increasingly efficient, but on the other, even a single faulty part can have more far-reaching effects than ever before. Faced with costly recalls, automotive manufacturers are confronted with increasingly complex requirements and stricter specifications. Is the effort of traceability worth it if it means labeling up to 20,000 parts per vehicle? Yes, it is, but powerful reading and verification technologies along with powerful software is needed to make sense of all the data.There are several reasons why manufacturers need to keep accurate records of the parts and components that make up a new car. From a quality perspective, for example, barcode tracking helps to ensure that the right parts are put together. Even more important, however, is the ability to trace each car part back to its original supplier. In the event of a recall or the discovery of a faulty part, manufacturers have to be able to quickly and comprehensively find out where each part came from. This is complemented by information such as batch number, date of manufacture and other important information to identify which vehicles are affected by a defective part. Recommendations and standards from AIAG, VDA, ANSI and ISO specify the details. As the automotive industry globalizes, worldwide production of light vehicles is expected to reach around 96 million units by 2023. This means that even a single faulty part can have an enormous impact, and therefore must be prevented at all costs.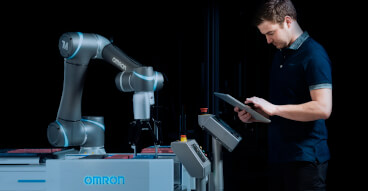
Lights out? Still unlikely with Industry 4.0
21 April, 2022 For many manufacturers, the prospect of a fully automated, human-free factory feels light years away. When, they ask, is the 4th Industrial revolution coming to us and what can we expect? In this blog, we look at the realities of (fully-/semi-)automated manufacturing, what robots can and can’t do, and why the human touch is still (mostly) irreplaceable.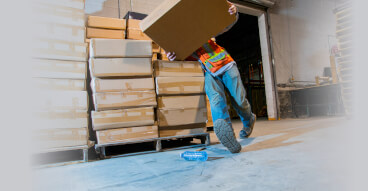
How the RB1200 Cobot Palletiser Can Simplify Your Automation Deployment
13 April, 2022 Greater automation and collaborative robotics (cobots) are the future for many industries, including logistics. Research by BMW found humans and robots work more than well together. In fact, human-robot teams were 85% more productive than working alone.It makes sense. Combining the speed and accuracy of robotics with the flexibility and intuition of humans compounds the benefits from each to build an unbeatable team.With the RB1200 Cobot Palletiser, OMRON, in collaboration with Reeco, is bringing a revolutionary new approach to end of line palletising. Creating an easy, flexible, safe, and compact solution to getting stock palletised and ready for transport.Palletising is a task perfectly suited to automation. The simple yet repetitive and physically demanding process of getting goods stacked leads to complications when performed manually. In 2019/2020, the Health and Safety Executive (HSE) estimated 19% of non-fatal workplace injuries were caused by handling, lifting, and carrying.Plus, given the labour shortages facing the UK and the wider world and the potential for spiralling staff costs, now is the ideal time to get your company less reliant on manual labour.While there are plenty of benefits to automating your palletising processes (greater output and accuracy, reduced labour and operational costs, etc.), its implementation also has challenges.However, with the RB1200 Cobot Palletiser, humans can collaborate with robotics on their terms, implementing a solution that fits their specific needs.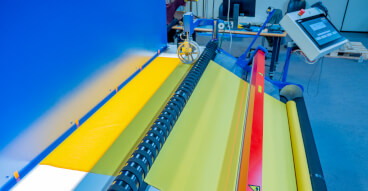
Vadain automates the inspection of curtain fabrics with machine vision
08 April, 2022 Vadain, the market leader in custom curtains in the Netherlands, needed a solution to detect errors as early as possible in kilometers of curtain fabrics. Together with software developers from Sycade, OMRON machine vision technology, and machine builder Eisenkolb, they developed an automated solution to detect and analyze errors in curtain fabrics, making the time-consuming manual inspection process a thing of the past.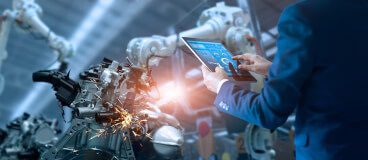
Discover How The CP1200 Case Packer Can Transform Your End-of-Line Manufacturing Processes
29 March, 2022 By Stuart Coulton, Market Development Manager, OMRON UK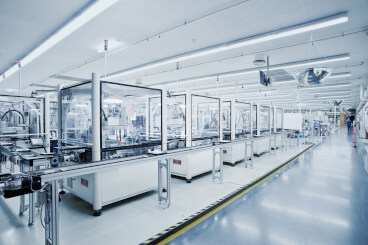
End of Line Automation: Now is the Time!!
29 March, 2022 By Stuart Coulton, Market Development Manager, OMRON UK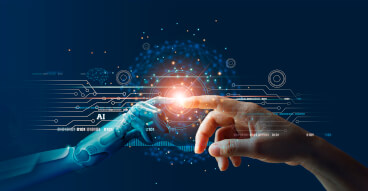
Traditional factories have data needs too
18 March, 2022 The right tools and tech can enable advanced predictive maintenance, bottleneck prevention and optimization. Find out how digitalization is bridging the gap between legacy systems and Industry 4.0.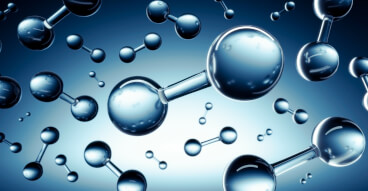
Fuel for the future: What to look out for in fuel cell production
10 March, 2022 When people talk about sustainable mobility, the first thing that comes to mind is battery-powered e-cars. Fuel cells or direct hydrogen burners are complementary technologies that often fade into the background, yet have a lot to offer when it comes to CO₂ reduction and market options.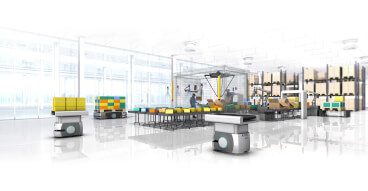
Mastering packaging and intralogistics challenges in eCommerce
24 February, 2022 Robot-assisted packaging enables fast and cost-efficient scalability upward and downward to handle swings in demands from the supply chain.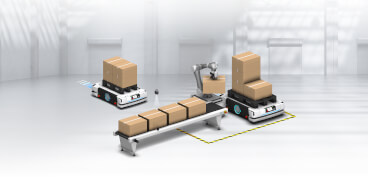
What to consider when selecting a mobile robot for heavy loads
11 September, 2020 Five questions to ask when selecting autonomous material transport technology for industrial applications.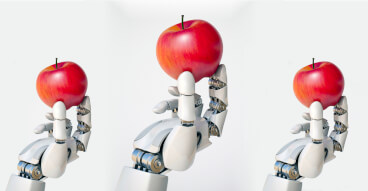
Factory automation: four tips for the future of food & beverage manufacturing
16 July, 2020 The coronavirus pandemic has posed major challenges to organisations of all types and sizes. In the food and commodity industry, companies have faced significantly reduced consumption and disrupted supply chains, while at-home consumption increased, and out-of-home consumption came near to a standstill. But how can manufacturers adapt their business strategies and production processes both now and in the longer term? The pandemic may provide an opportunity for rethinking outdated processes and procedures and enhancing them with concepts such as innovative robotics, sensor technology and holistic automation strategies.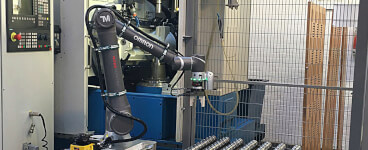
Cobots give gear manufacturer a competitive production edge
14 May, 2020 Danish gear manufacturer, Fischer Gears, has boosted the competitiveness of its production process - especially on larger series – by installing two OMRON TM robots. The collaborative robots (cobots) free experienced employees to focus on more value-adding tasks.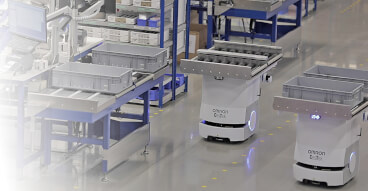
Made-to-order production with an advanced fleet of mobile robots
11 May, 2020 VOLA, a Danish manufacturer of luxury sanitary and kitchen fittings, has opened a new factory that incorporates a fleet of nine mobile robots from Omron.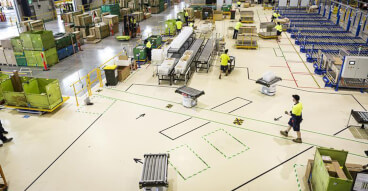
Mobile robots smarten up Toyota’s new parts centre
28 April, 2020 Intelligent robots and sophisticated design are helping Toyota to achieve a higher level of efficiency at its new warehouse in Sydney, Australia.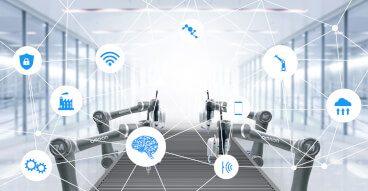
Cobot and flexible production - Future-proofing SMEs?
17 March, 2020 Many countries in Europe, such as the UK and Germany are likely to experience serious labour shortages over the coming decade, especially in relation to technical specialists. At the same time, product lifecycles are becoming shorter. Despite this, small and medium-sized enterprises (SMEs) might be reluctant to invest in additional automation. However, collaborative robots (cobots) are easy to set up and offer a quick and cost-effective solution. They can increase the flexibility, quality and speed of production and enable companies to respond rapidly to changing market conditions. Omron’s TM series of cobots are a good example of this versatility.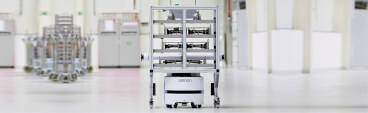
ŠKODA AUTO uses LD mobile robot at Vrchlabí plant
17 March, 2020 The autonomous robot contributes to the continuous improvement of work safety in Vrchlabí and helps to minimise work risks. It recognises people crossing its path as well as other vehicles and stationary obstacles.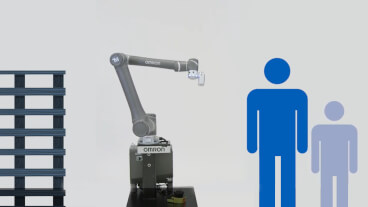
Safety in collaborative applications
10 February, 2020 Collaborative robots can be used in a wide range of industrial applications. Thanks to various integral safety features, they can work safely with or near people. In addition, they can easily adapt to changing needs. This results in increased productivity, especially in repetitive tasks, enabling manufacturers to reap the benefits of a high return on their investment. However, for a cobot application to be successful, it must incorporate safety considerations based on comprehensive risk assessments. So, what are the industry safety standards and solutions that will enable a company to gain the maximum value from cobots within a collaborative workspace?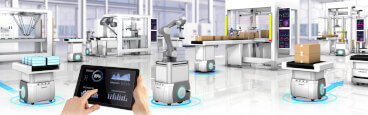
The factory of the future: people and machines working together in harmony
20 January, 2020 Automation and artificial intelligence (AI) are transforming the efficiency of industrial production, through stronger interactions between man and machine that can boost productivity. A new, promising model for ‘factory harmony’ is based on intelligent, integrated and interactive design for tomorrow's manufacturing processes.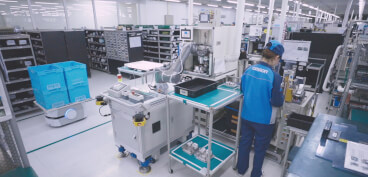
Humans and machine collaborate to meet today’s challenges
23 December, 2019 In Shanghai, labour costs are increasing by 7% every year. With growing shortages in manpower, it is becoming more and more difficult to hire factory operators. On the other hand, companies must consider return on investment and equipment effectiveness when adopting automation solutions in the factory.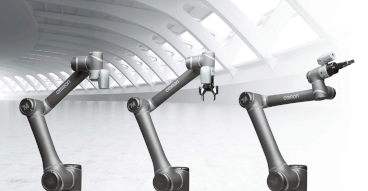
Three pillars of successful cobot deployment: safety, quality and flexibility from a single source
04 November, 2019 The use of collaborative robots is expected to increase rapidly in the next years to meet the needs of flexible production lines. To ensure that manufacturing layouts can be easily adapted to changing customer requirements, we recommend teaming up mobile robots and cobots. In addition, companies must consider integrated software apps and vision technology, as well as ensure support and risk assessment.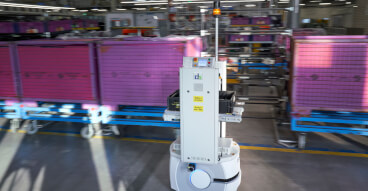