How Remote Connectivity can help your company through challenging economic times
Published on 27 February, 2023 in Industry 4.0
What was supposed to be a period of recovery for the manufacturing industry post-pandemic has turned into anything but. Labour shortages persist, except now they’re compounded by high inflation, a looming recession, the conflict in Ukraine, and political mayhem at home. It can feel like every day brings another challenge to overcome. UK manufacturing was already at an inflection point, with businesses looking to transform their operations, introduce new technologies, and find ways to increase automation. Unfortunately, this can require an injection of capital that is harder to find at a time of financial uncertainty.
As we round out 2022 with our third government of the year, we are still not sure how the new premiership of Rishi Sunak plans to solve the black hole that is the nation’s finances. But one thing is for certain, costs will rise, and UK manufacturing has a tumultuous road ahead. However, even when market conditions are tough, opportunities remain. In this blog, we will discuss the challenges of investing in new machinery, particularly given the economic outlook and how remote connectivity can help maximise its use while also minimising operational costs.
The risks of investing in machinery given the current economic climate
The need for new machinery and greater technology within manufacturing is driven by many factors, with labour shortages chief among them. According to the Office for National Statistics (ONS), from July to September 2022, there were 450,000 more vacancies in the UK compared to the pre-Covid levels (January to March 2020), an increase of 56.6%. The labour shortage remains 10.3% higher than it was a year ago, with 117,000 more vacancies.
However, there is a glimmer of hope with a 46,000 decrease in vacancies in Q3 2022 compared to Q2. The first significant drop since the start of the pandemic.
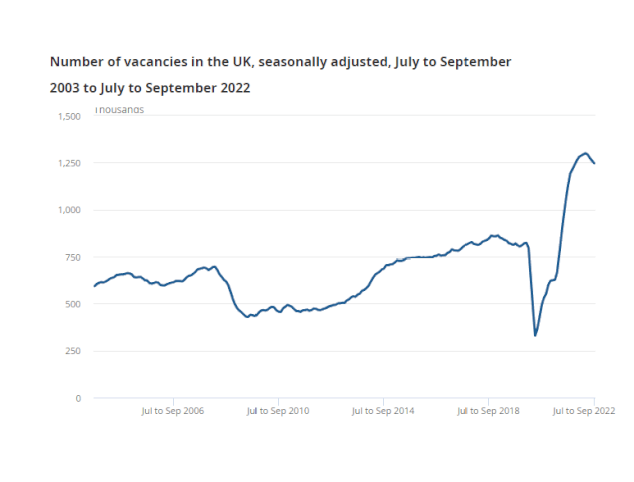
With fewer workers available, businesses looking to maintain or increase output are turning to technology. A 2021 survey found 25% of companies with warehouse, fulfilment, production or distribution operations have accelerated their automation plans. 73% surveyed also stated automation is business-critical for them moving forward. So how will this transition succeed, given the worsening economic conditions in the country?
Rising expenses mean manufacturers can either take the hit themselves and reduce their margins or pass the price increase on to their customers. However, with the whole country going through a dramatic cost of living crisis:
- In October 2022, the Consumer Prices Index found prices were 11.1% higher than a year ago.
- Energy bills have skyrocketed since the Russia-Ukraine conflict, with the price of gas increasing by 129% and domestic electricity by 66% from October 2021 to October 2022.
Households will struggle to absorb the cost increases for all their goods, meaning they will cut back, and demand will drop. This places significant strains on organisations looking to invest in their machinery. Understandably, investors want to see a clear return on investment when making significant outlays. With uncertainty around the demand for certain products, it is more complicated than ever to make accurate predictions moving forward.
This can result in an endless negative feedback loop:
- Businesses need predictable demand to justify the investment
- Without new machinery, you need labour to fill existing demands
- With labour shortages, you need to invest in new equipment
- Rather than becoming trapped in a stalemate, organisations can now look to other technologies that help tip the scales in favour of investment.
Remote Connectivity: An old friend bringing new opportunities
- Predictive maintenance via data analytics - Acquiring and analysing data to optimise maintenance schedules, predict errors, and ensure machinery is always operating at 100%.
- Production-as-a-service (PaaS) – Taking the idea to the extreme, PaaS effectively allows businesses to subscribe to a factory. Instead of owning facilities and incurring all the overhead costs that come with it, they can outsource manufacturing needs to a specialist with cutting-edge machinery and practices that bring their product to life.
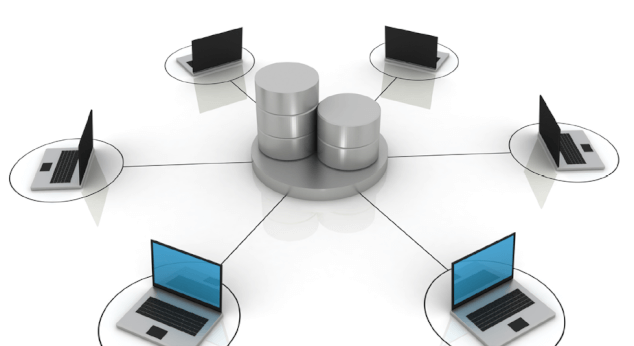
Conclusion
The outlook does not look ideal, but there are opportunities for manufacturers willing to invest in the right technologies for their situation. Remote connectivity maximises the impact of new machinery, putting the data it produces to work for you.
Finding employees remains a considerable challenge, and investing is complicated by the economic situation. You can muddle through, work hard, and hope for the best or you can work smart with technology optimising production and powering decision-making.
It is also critical to remember that incorporating technology is not a silver bullet capable of propelling the industry forward on its own. Instead, a significant change in mindset is also required to help get the economy back on track and realise the untapped opportunities that exist.
Discover more with our new Remote Connectivity White Paper