4 Steps to Optimise Manufacturing Operations Using Production Data
Published on 17 April, 2023 in Operational Excellence
Bottlenecks and other production issues are the scourge of efficiency, costing businesses thousands, if not millions, a year through delays, disruptions, wasted resources, and lost output.
Based on your assets (staff, equipment, facilities, etc.), what should your business be capable of producing?
Most businesses have at least done a back of an envelope calculation on what their optimum output could be, if not taken the time to do a detailed analysis breaking down every process in the production chain. How far off is your actual throughput compared to the best-case scenario?
In highly competitive markets with shrinking margins and a challenging economic forecast, businesses have to find ways to maximise their operations, getting as close as possible to optimal performance. They can no longer accept inefficient processes such as:
- Unbalanced assembly lines
- Long changeover times
- Minor discrepancies compounding to increase the failure rate
- Poor equipment efficiency or extended maintenance downtime
- Untrained staff slowing production
Thankfully, manufacturing has come a long way. With the integration of new technologies (robotics, IoT, AI, etc.), companies can generate and track considerable production data.
However, having data is just the start. To impact your operations for the better, businesses must derive actionable insights from it. Listed below are four steps to help businesses identify and resolve production issues.
1. Assess your current production situation
To start with, you must take a deep dive into your existing production workflow. Surveying how work is currently performed, including where and how data is being collected, production budgets, changeover times, unplanned downtime, etc.
Production should be broken down into a series of interconnected and independent tasks. Often each of these will require specialised equipment and trained staff. To minimise delays, it is important to understand the critical path, i.e., the longest sequence of sequential tasks that have to be completed. These tasks are the most time-sensitive, with any delay creating a knock-on effect delaying the delivery of the final product.
From this information, you can identify any gaps regarding data and begin to draft potential improvements.
2. Data collection and analysis
The next step requires extensive data analysis to build a clear picture of where current production processes are falling short. Organisations can uncover previously undiagnosed production issues and build an implementation roadmap to resolve them.
Analysis links data with critical problems in the production process. Developing models to determine correlations in the data that could not otherwise be detected.
3. Begin improvement implementation and monitor results
Once potential improvements have been identified and implemented, production must be monitored to assess the effectiveness of the solution. This involves building effective dashboards to continuously track key processes and further incorporate data where possible to uncover new opportunities for innovation.4. Review & Iterate to drive future innovation
Unfortunately, staying on top of production issues is not a one and done process. It requires regular review and iteration to stop inefficiencies from creeping back in.
While this means repeating the cycle, with improved data collection in place and experience with analytics, you can improve yourself along with your production processes. Learning to quickly identify deviations in the data, spot new issues, and develop the solutions needed to take production to another level.
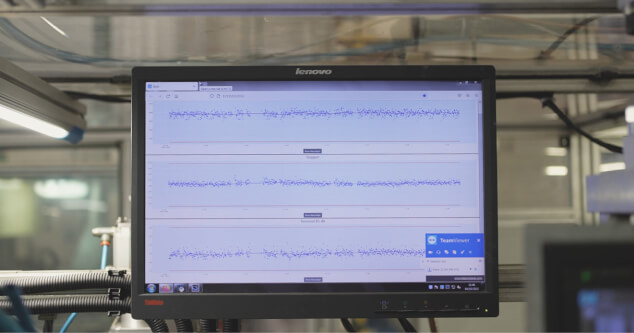
Conclusion
Production issues prevent businesses from maximising their potential. But with data on your side, you can shine a light on every part of your operations to track down waste, wherever it may be.
At Omron, we have years of experience converting data into insights. Our manufacturing and data experts have years of experience identifying and fixing manufacturing issues. With our knowledge and your understanding of the company and its goals, we can collaborate to co-create a technologically advanced and sustainable manufacturing operation.
We work to deliver realistic, flexible, and people-friendly production processes that can quickly adapt based on:
- Customer input
- New data insights
- Cutting-edge technology
Omron’s i-BELT Data Services provides a full examination resource in four value-adding categories: manufacturing, quality, equipment, and energy, to tackle any and every production issue you face. We input production data and, through visualisation and analytics, output improvements suited to different phases and customer needs.
Today, UK manufacturing companies are facing considerable challenges. From growing labour shortages and the lack of skilled talent to rising raw materials and energy costs, manufacturing companies must strengthen their production processes to remain viable.
OMRON can guide you through the process from start to finish and help you unleash the true potential of your factory. To get started, you can set up a short, 15 minute chat with one of our experts to see if it can work for you.
Sign up here