Fuelling the success of local battery cell production
Published on 20 September, 2021 in Sustainable Manufacturing
What should automotive and battery production companies pay attention to in order to make their production more innovative and competitive? Here are five tips for more future strength for the industry.
Expert and automotive manufacturers alike agree that e-mobility is the future. Batteries and battery manufacturing are central to this development. In this context, the global market for lithium-ion batteries is expected to grow from 44.2 billion US dollars (2020) to 94.4 billion dollars (2025). The transformation of the automotive industry from internal combustion engines to battery or hydrogen-powered fuel cells is presenting companies with immense challenges.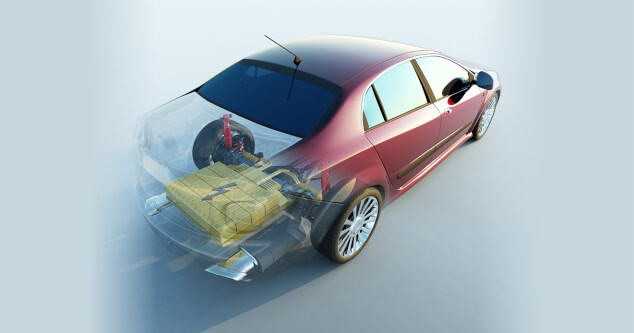
Sustainability is key in battery production "made in Europe"
According to current research, most of the battery cells used worldwide still come from production facilities in Asia. Politicians and business will want this to change soon in order to strengthen the competitiveness of the European e-mobility industry. In Germany for example, the Federal Ministry for Economic Affairs and Energy is funding research and development projects from industry-led associations as well as individual industrial projects.Smart Factory: Venture new production models and technologies
Smart Factory, summarized as future-oriented and flexible concepts for the manufacturing of the future with well-known topics such as continuous digital supply and value chains, more agile process flows as well as the close connection of production, quality (avoidance of rejects and waste), customer needs and life time traceability harmonize. These are all tools to be able to survive in the market, to act more profitably, more sustainably, faster and safer, to stand out from the competition. There are also other trending topics such as digitization, track and trace, value chain participation and improved networking. Predictive maintenance, predictive quality, integrated production planning and process visualization will also be taken into account in the smart factory of the future. OMRON answers this need with its innovative-Automation! Model.
Five tips for more future strength:
What should automotive companies pay attention to in order to make their production more innovative and competitive?- Rely on edge computing: Machines can be coupled better than ever before, and data can be collected, structured and analysed at the edge using powerful sensor technology.
- Use sensor technology: Remote services and the integration of additional sensor technology for missing data points, machine identification, cybersecurity, but also the use and conversion of data and communication protocols are advisable.
- Drive human-machine collaboration: Mechatronics and IT solutions are increasingly merging and, in interaction, support more efficient and flexible production processes. Concrete examples of applications are smart new industrial robots, mobile robots but also cobots that work hand in hand with the employees in the plant.
- Bring together components of modern production processes in the cloud: By doing so, you benefit from central and transparent monitoring of all machines, systems and components through control based software modules or cloud-based functions, for example in terms of asset management, condition monitoring, predictive maintenance or remote services.
- Use Augmented Reality (AR) as a further building block of the smart factory: You can gain additional computer-generated information and virtual objects complement live images or videos, which gives you an extra level of information, support and know-how.